Fire and lithium batteries: the manufacturer’s role in safety
31 August 2022
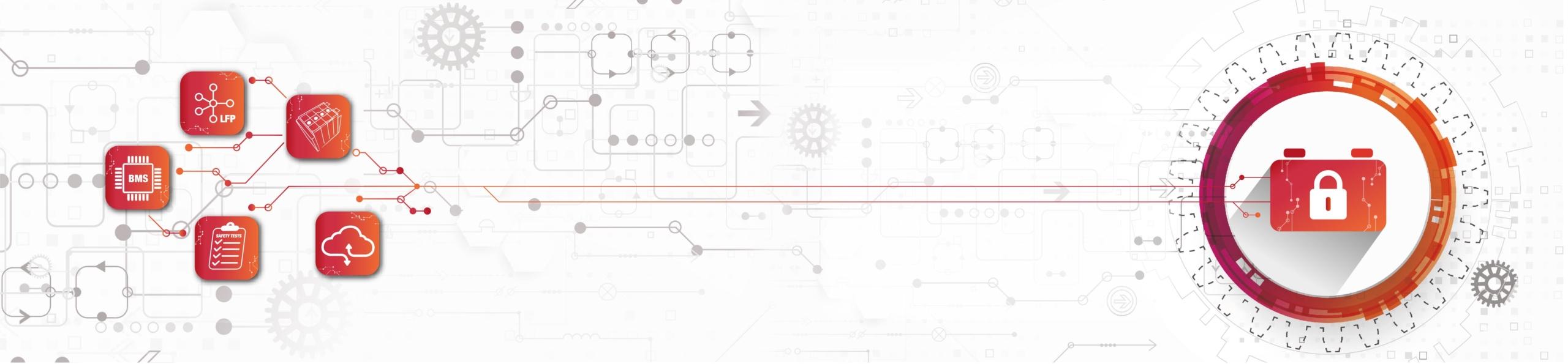
The energy transition is underway and attention turns to batteries, essential in order to completely free ourselves of fossil sources and embrace electrification.
This spotlight on the world of batteries has led to an increase in laboratory experimentation, but has also aroused the interest of the general public. And when the public takes an interest in scientific and technical matters, it’s easy for inaccurate ideas, generalised beliefs and unfounded fears to circulate. The most resounding example is the circulation of the (mistaken) belief that “lithium batteries are highly flammable”.
In terms of a lithium battery’s flammability, the lithium battery manufacturer plays a key role and can do a lot during the design, material selection and construction phases to ensure batteries are safer and therefore minimise the risks.
Lithium batteries are made with small cells, you have to use a very high number of parallel cells. Consider a 400Ah battery. If it’s comprised of 3Ah cylindrical cells, then 130 parallel cells would be needed, but if it’s made up of 50Ah prismatic cells, then only eight parallel cells are required to achieve the desired capacity. So if one of these cells were to have a problem and short circuit, in the first case it would have to absorb energy up to 130 times its capacity, while in the second case it would be only eight times.Flash Batteries are produced with a maximum of four parallel cells. According to our studies and tests, this is the best configuration in which our batteries can guarantee safety in every situation.
Battery electronics
Battery Management System software allows for the chemistry to be fully exploited, ensuring reliability and performance over time.
The electronic control unit (the BMS) monitors the power and temperature of the individual cells and communicates with the vehicle hosting the battery and with the battery charger, to block charge and discharge in case of any criticality and intervene on the general contactors. The BMS, if designed carefully and thoroughly, ensures performance stability over time, prevents any anomalies, and carries out self-diagnostics and predictive maintenance, for complete control of the battery pack. Flash Battery has focused on electronics from the very beginning, developing a patented, one-of-a-kind BMS and a proprietary remote monitoring system with numerous advantages: the Flash Data Center.
The Flash Data Center among the finalists at the Bauma Innovation Awards
This is one of the reasons why we developed the Flash Data Center, a proprietary platform that automatically and remotely analyses all the charge and discharge cycles of interconnected batteries on a daily basis. This remote monitoring is subject of an Italian patent and currently under consideration for a European patent. The system has been considered so innovative, efficient and well-received that it was nominated as a finalist at the Bauma Innovation Award.
As a matter of fact, Bauma 2022 will be the showcase for Flash Data Center 4.0, the new release that applies artificial intelligence and ensures interconnection of all battery systems produced by Flash Battery with the support of advanced machine learning technologies.
Our goal is to identify the safest chemical for the client’s vehicle. Our technicians in the R&D department do not just limit themselves to using cells certified by the manufacturers or the theoretical study of chemistries, but also base their decisions on the various specific tests with the aim of “stressing” the batteries and identifying possible improvements. One of the most invasive tests, for example, is the Nail Penetration Test, which consists of perforating a battery with a nail, simulating an incident that causes an internal short circuit.
The lithium batteries (single cells or complete batteries) undergo two types of tests, safety tests (including abuse tests) and performance tests.
Safety tests
Lithium battery production companies should test batteries’ safety by subjecting them to operating conditions close to the declared limit (or even outside of the normal range), to be sure that a minimum level of safety is guaranteed for those using and transporting them, even in extreme conditions.
A group of standard tests known as UN38.3 (from the paragraph in the “Manual of Tests and Criteria” that outlines the methodology) constitute a basic requirement for the safe transportation of batteries, and this is required worldwide for carriage by road, ship and air.
The abuse tests that we conduct to “stress” the batteries and experiment with updates include the Nail Penetration Test, which consists of perforating a battery with a nail to simulate an internal short circuit.
Of course, these are tests that are carried out in safe and controlled conditions at a laboratory, and the chances of a cell being penetrated during general use when a lithium battery is installed on an electric vehicle or industrial machinery is very low. But we include this test, because it simulates the worst case scenario of what can happen to a cell, or rather an internal short circuit that can occur due to a manufacturing defect or violation.
Performance tests
Performance tests serve to verify battery performance but also to compare the nominal specifications of batteries, in an objective way, with other batteries of the same type available on the market.
Following a significant rise in the use of lithium batteries in the automotive field, testing activities by lithium battery companies for this type of accumulator have increased dramatically in recent years.
Until a few years ago, there were not many laboratories equipped for the testing of medium/large batteries (or rather, sizes differing from those of single cells and portable devices). But in recent times, a number of different laboratories have been set up in Europe and, in the last year, significant investment has been made in Italy to create laboratories suitable for the execution of these specific tests.