Modular or custom batteries? Pros and cons
13 April 2021
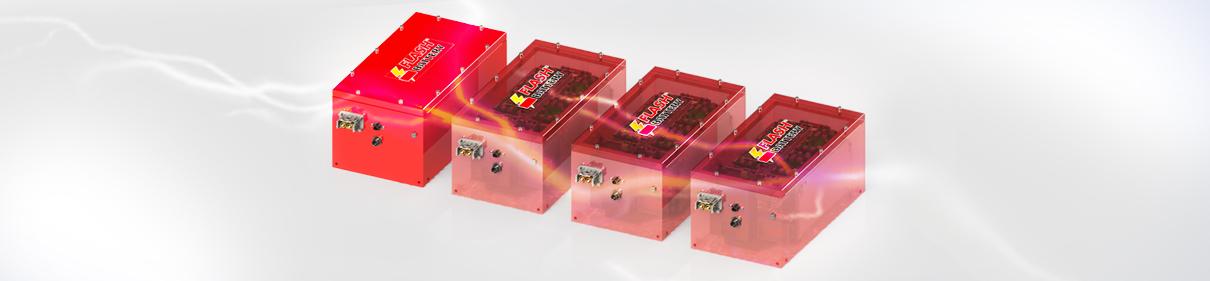
Our R&D department has developed mostly custom lithium batteries over the years. We examined the requirements of each project and developed solutions specifically intended for the application.
Our battery customisation procedure is a single and simple work method. The well-established process starts with a feasibility study by our engineers, who analyse the specific requirements (work cycles, field of application, voltage and capacity) so that the available energy is an exact match to what the application needs.
Every step of this customisation process was applied to the over 15.000 lithium batteries we have produced to this date.
Sometimes, however, manufacturers have a need to equip their machine with varying ranges and this is where modular batteries come into play to solve that need.
A modular system is typically a firmware functionality that enables us to install parallel battery modules within the same application.
With this installation, each module can be configured as a stand-alone battery, either as a master battery or a slave battery.
To make this system simple and accessible to manufacturers, we developed a free tool that with a wizard and in just a few clicks guides the manufacturer through the installation of the modular batteries.
The guided procedure configures the modules automatically, creating a single “virtual” battery (single battery code) of greater capacity. This also gives the added advantage of monitoring the battery as a unit via the Flash Data Center.
A modular system can be useful when the application already contemplates very high capacities (normally above 600 Ah) and when breaking up the capacity into smaller parallel battery packs (e.g. 300 Ah) does not incur additional costs.
When manufacturers have several products in production, each one with its specific energy needs, like for example, a range of vehicles with different range requirements, they could use a single module for the small vehicle and two or three modules for the larger one.
This solution would enable manufacturers to purchase just one battery code for every application, simplifying the supply chain.
The poor flexibility of modular systems
Modular systems use several parallel battery packs inside the application, without distinction. The batteries are standard and of equal size; one is the same as the other.
Sometimes this can be a problem.
In fact, modular batteries require a greater degree of flexibility on the vehicle/machine side. This means the manufacturer has to necessarily find the space in its product to house the standard modules by moving whatever is in the way.
If, mechanically, the vehicle/machine does not allow for this kind of adaptation, then the most effective choice would be to use a custom battery pack. In this case, the geometry of the battery is adapted to the available space, without having to make any changes to the product.
In addition, custom battery packs can be adapted to the vehicle’s/machine’s electrical requirements as well, such as, for example, by integrating more inputs and outputs or including special functions like precharge or insulation control.
Contrastingly, with modular batteries optional features are avoided because their cost applies to each module, so this basically translates into less flexibility in terms of interconnections and specific functions.
Every time we produce low-capacity lithium batteries and install several of them in parallel, we have to take into account the “fixed costs” of each individual battery.
For example, a 10 kWh battery has the same electronics as a 20 kWh battery pack, so if we use two 10 kWh battery packs, BMS, safety, communication and any other function double … that could cause a hike in the overall cost of the energy “reservoir”.
Every application has its own specific requirements and needs.
The role of Flash Battery is to work alongside the manufacturer in the most difficult part of the process, i.e., choosing the best solution for each application.
You might not know it, but analysing each detail of your product – the type of application; its consumption, size and space; the context and mode of use, etc. etc. – can make a difference and is crucial in giving birth to the perfect lithium battery for you.
Every piece of information is essential to develop the electrification project most suited to your needs and this is why choosing a supplier with the right know-how and experience plays a strategic role, especially for manufacturers that are now entering this market and converting their models.
Our team of engineers and specialised technicians will be by your side from the very start to assess the solution that can best suit your electric vehicle or industrial machine.