Which chemistry is most suitable for the electrification of your vehicle? Let’s discover the different types of batteries
30 June 2022
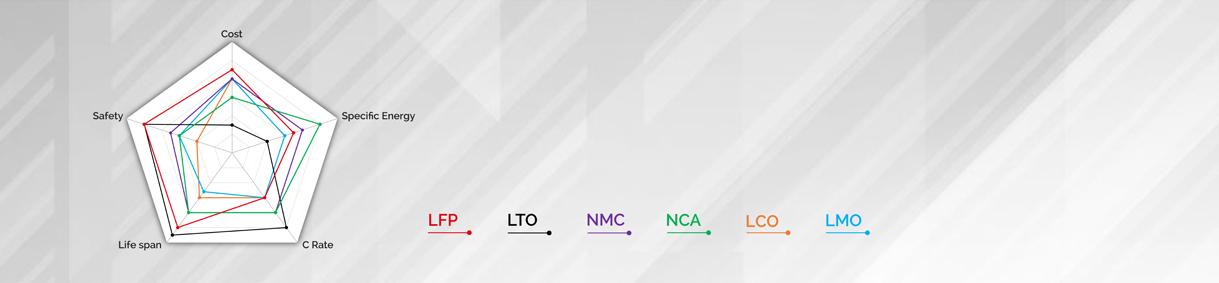
Today, lithium batteries are being used for the electrification of an increasingly wide range of applications. While they initially involved telephones, computers and small tooling applications, they have gradually evolved towards the electrification of hybrid or full-electric vehicles, and today a growing number of manufacturers of industrial machines and electric vehicles are turning to this technology for the electric transition of their fleets, in a wide variety of sectors, such as logistics, material handling, construction, aerial platforms, agriculture, airport vehicles and shipping, to mention only some of them.
Now more than ever, therefore, choosing the right lithium battery for your vehicle has become a complex but necessary task, especially in view of the latest provisions from the European Parliament, which has approved a ban on petrol and diesel car sales from 2035.
Lithium batteries, however, are not all the same! There are many elements that go into creating the most suitable battery for a specific application. Many different types of lithium batteries are available on the market; but behind the voltage, Ah and size of a lithium battery there is really a complex way, made up of study, research and development, technical tests and above all, the choice of the right chemistry, which may or may not be more or less suitable for the needs of your vehicle.
We will take a closer look at the six main types of lithium batteries and their construction chemistries:
Composition and characteristics of lithium batteries with LCO chemistry:
Lithium – Cobalt – Oxide (LiCoO 2 )
Lithium batteries with LCO chemistry are the least recent, mainly used for electronic devices and mobile applications, and consist of a cobalt oxide cathode (positive electrode) and a graphite carbon anode (negative electrode).
The advantage of this chemistry is that it has a high specific energy and is perfect for medium-small batteries, that are able to perform well, so that they can be charged very quickly.
LCO batteries are in fact the most widely used for smartphones, digital cameras and portable laptops.
On the other hand, their use is mainly limited to applications that are not too large due to their safety limitations. They furthermore feature a rather low discharge current and this can lead them to overheat quickly under high loads. They also contain a high proportion of cobalt, an expensive element that is difficult to find and associated with major ethical problems in extraction, and this is why an increasing number of manufacturers are now trying to do without it or limit its use as much as possible.
- Rated voltage: 3.6 V
- Gravimetric density: 200 Wh/Kg
- Energy density: 400 Wh/l
- Complete life cycles: 500 – 1,000
- Discharge rate: 1C
Composition and characteristics of lithium batteries with LMO chemistry:
Lithium – Manganese – Oxide (LiMn 2 O 4 )
Lithium batteries with LMO chemistry perform very similarly to those using LCO technology. They are widely used in small devices such as power tools.
The main characteristic of LMO batteries is their ability to provide much energy in a short time. LMN batteries consist of a manganese oxide cathode and a graphite anode.
They are often used for electric bikes, in gardening, medical equipment and power tools such as drills and screwdrivers.
LMO batteries have a higher thermal stability than batteries with LCO chemistry, but are limited by their capacity, which is lower than cobalt-based systems.
- Rated voltage: 3.7 V
- Specific energy: 150 Wh/Kg
- Energy density: 350 Wh/l
- Complete life cycles: 300 – 700
- Discharge rate: 1C, 10 C
Composition and characteristics of lithium batteries with LFP chemistry:
Lithium – Iron – Phosphate (LiFePO4)
LFP chemistry responds best of all to the specific needs of the industrial sector, where excessive specific energy is not required, but where there is a need for very high safety and long life cycles. So we are talking about a very wide world, ranging from automation, robotics, logistics, construction, agriculture, boating, electric vehicles, to airport vehicles, aerial platforms and special vehicle
In fact, batteries with LFP chemistry are the safest and most stable on the market today, and are available in large-capacity formats, as required by industrial systems, without the need to connect many small cells in parallel, which would lower their stability and compromise the safety of the vehicle.
The life cycles in a battery with LFP chemistry today exceed 3,500 cycles and, if equipped with a good BMS system, can easily exceed 4,000, and in the future even more than 6,000 cycles may be expected.
But we must be careful, when we talk about “life cycles” we must not think that after 3,500 cycles a battery is completely exhausted. In fact, it is important to remember that the end-of-life of a battery on a vehicle is always considered to be 80% capacity remaining, but there will still be plenty of possibilities for use in other areas, such as energy storage.
Another advantage of LFP chemistry, besides its inherent safety and high life cycles, is that it has a flat discharge curve. In the image below, the curve tends to rise. This is the so-called charging curve, while the descending curves refer to the battery voltage during discharge. The voltage range from 100 % to 0 % is therefore very similar, and this is a fundamental fact, as it allows machines and industrial vehicles to guarantee the same performance from the beginning to the end of the discharge.
- Rated voltage: 3.2 V
- Gravimetric density: 177 Wh/Kg
- Energy density: 384 Wh/l
- Complete life cycles: > 4000
- Discharge rate: 1C/3C
On the other hand, this advantage can also turn into a disadvantage, as, due to the flat curve, reading only the voltages will make it more complicated to determine a correct SOC (state of charge). To avoid this limitation, the BMS system managing the battery will have to be designed in a smart way to provide the correct State of Charge and perform the balancing functions in the best possible way.
One of the many advantages of this chemistry is the total absence of cobalt, a material which, as we have already mentioned, is toxic, one of the most impactful for the environment. Many lithium battery manufacturers are currently trying to reduce the percentage of cobalt in their batteries, so the LFP chemistry, being cobalt-free, starts with a big advantage.
Although only a few years ago, LFP batteries seemed to have been destined to be forgotten, as their energy density was very low, at around 100 Wh/Kg, today this technology has literally re-emerged from the ashes with a very significant increase in energy density, reaching 170 Wh/Kg in a short time, prompting strong interest from the automotive world. Further increases in gravimetric density to 220/230 Wh/Kg are already expected in the coming years.
This is exactly why many car manufacturers have decided to reintroduce LFP chemistry for the electrification of their vehicles, first and foremost Tesla, which is currently using it in its “standard range” vehicles as it guarantees a better level of safety, at a slightly lower cost than the NMC chemistry used for high-performance vehicles. Like Tesla, also BYD, Volkswagen and many other major automotive manufacturers now see great potential in LFP chemistry.
Composition and characteristics of lithium batteries with NMC chemistry:
Nickel – Manganese – Cobalt (LiNixMnyCozO2)
To date, batteries with NMC chemistry remain the most frequently used in the automotive sector.
With this chemistry, a very high specific energy of up to 220 – 240 Wh/kg can be achieved. This is clearly a decisive competitive advantage for a car, as it allows a large amount of energy to be stored with a low weight and volume, allowing more energy to be installed in the vehicle than other lithium-based technologies.
There are various types of NMC chemistry:
- NMC 111 (Nickel 33.3% – Manganese 33.3% – Cobalt 33.3%)
- NMC 622 (Nickel 60% – Manganese 20% – Cobalt 20%)
- NMC 811 (Nickel 80% – Manganese 10% – Cobalt 10%)
- Voltage rating 3.6 V
- Gravimetric density: 220 Wh/Kg
- Energy density: 500 Wh/l
- Complete life cycles: 2000
- Discharge rate: 2C/3C
There are three numbers following the abbreviation NMC indicating the percentage of the elements used for the cathode. NMC 811s are the newest: they have a high nickel concentration and a very low manganese and cobalt content. This results in higher energy density at a lower cost. By contrast, more common are the NMC 622 cells and, now rarely used, the older 111.
It is therefore clear that NMC technology, in its evolution, has likewise set itself the ambitious goal of reducing cobalt as much as possible, but this is still a very laborious process, because cobalt is an element that gives stability to the system and increases life cycles.
Research does not stop, however; on the contrary, there are already companies experimenting with innovative new technologies in this respect, such as Svolt for example, which recently announced the first NMX cell, completely free of cobalt.
Composition and characteristics of lithium batteries with NCA chemistry:
Nickel – Cobalt – Aluminium (LiNiCoAIO2)
Batteries with NCA chemistry are also used in the automotive sector alongside with NMC batteries. Their safety rating is slightly lower than that of NMCs, but at the same time they have a very high energy density, reaching 250-300 Wh/Kg. The NCA cell structure is very similar to that of the NMC 811, with a high nickel content and a low cobalt and aluminium content.
Due to their high energy storage capacity, NCA lithium batteries are often used in blends with NMC chemistries to achieve a compromise between energy density, safety and stability.
- Voltage rating 3.6 V
- Gravimetric density: 250 Wh/Kg
- Energy density: 550 Wh/l
- Complete life cycles: 1000
- Discharge rate: 2C/3C
Composition and characteristics of lithium batteries with LTO chemistry
Lithium titanate (Li4Ti5O12)
It is a chemistry that is still little mentioned, but it appears to be very promising in terms of life cycles, as its low internal voltages and lack of mechanical stress allow it to degrade very little, easily reaching 15,000 to 20,000 cycles. Because of this particular advantage, it could be used for the electrification of cars and vehicles subject to very heavy use, but at present it still carries some problems that limit its use and diffusion.
Its weak points are 2:
The low energy density (177Wh/l) and gravimetric density (60-70 Wh/Kg) as well as a lower nominal voltage of 2.4 V or 2.8 V: this means that more cells will be needed in series to achieve the desired battery voltage. Its currently very high cost which is reflected in a low number of global LTO cell manufacturers, this probably due to the current low volumes demanded by the market
Its advantages, on the other hand, include not only its long service life, but also its wide temperature range, and its excellent susceptibility to high-power charging and discharging, i.e. high C-Rate (ratio of current to rated capacity).
The ideal use of LTO technology are heavy-duty applications such as AGVs (automated guided vehicles): imagine fleets of self-driving forklift trucks working 24/7, which also take advantage of fast charging to reduce downtime and consequently increase plant efficiency.
- Voltage rating 2.4 V
- Gravimetric density: 70 Wh/Kg
- Energy density: 177 Wh/l
- Complete life cycles: 15000 – 20000
- Discharge rate: 4C/8C
We have outlined the 6 main types of lithium-based chemistry that are currently most widely used in the various electrification areas. But we must not think that these chemistries are in competition with each other, quite the contrary! They are all valuable and high-performing, but each lithium chemical works best in different areas of use.
This diagram shows a comparison of the various characteristics of the chemistries in terms of:
- Specific Energy or Gravimetric Density [Wh/Kg]: is the ratio of the amount of energy contained (Wh = V x Ah) to the weight of the battery.
- Safety: which is closely related to thermal stability because intrinsic safety depends very much on how thermally stable the components are
- C- Rate: charge/discharge rate, i.e. the ratio between the charge or discharge current (A) and the nominal capacity of the cell (Ah). This is a parameter closely linked to the cell’s ability to generate power.
- Life cycle: Number of times the cell can be discharged and charged until the end of life is reached, normally considered when 80% residual capacity is reached.
- Cost
How to choose the most suitable type of lithium chemistry
We therefore try to explain in detail why one chemistry or the other should be chosen depending on the type of application to be electrified.
NMC and NCA batteries for the automotive sector
Why are NMC and NCA more widely used in the automotive sector? Because this requires a very high energy density, which can give a great power in a small space. Thus, in electric mobility, energy density, gravimetric density and specific power are essential elements, where charging speed is considered a key focal point, together with high acceleration power, particularly in premium models. Other performance features such as, for example, high battery life cycles are therefore not crucial in this sector, simply because they are not necessary!
A car is in fact extremely unlikely to make several cycles in the same day, if not a few days a year in the case of a long journey. On the contrary, a car normally uses only 20-30% of its charge in a day.
If we take, for example, a Tesla that can travel more than 400 km on one charge: if we consider a useful life of 400,000 km, this means that the total cycles that the battery has to endure will only be 1,000 ( 400,000 / 400 = 1,000 cycles) This explains why the life cycles for a battery with NMC chemistry do not exceed 2,000 (even less in NCA chemistry, where the life cycles are up to 1,000).
LFP and LTO batteries for the industrial sector
In industry, agriculture, or even for the electrification of special vehicles, especially if it is about highly cyclic applications that put stress on the battery, it is better to use chemistries such as LFP and LTO, where service life, reliability and safety are the most important requirements.
In the industrial world, therefore, the issue of space is less of a constraint, just as it is not essential to have excessive performance or energy density. When evaluating the choice of the right chemistry, the more important factor of safety therefore comes into play, an aspect that few people want to, and can, compromise on.
It is better to have a battery that is slightly bulkier, but provides optimum safety and has a significantly longer service life. There are vehicles, such as LGVs and AGVs which are required to be used intensively and work incessantly around the clock, as a result, their batteries will even do 3 or 4 charging cycles in a single day. The LFP chemistry will therefore easily support them with its more than 4,000 recharge cycles.
If batteries for stationary storage are necessary, then energy density would mean almost nothing, and, on the contrary, battery cost and life cycles would be the elements behind the choice of the chemistry. LFP chemistry would then find its place.
LCO and LMO batteries for small mobile applications
Ultimately, if a very small battery is needed for use in tools and mobile applications, then its main characteristic must be its light weight, otherwise the performance of the entire application will be affected by too much weight. In this case, it will be possible to choose chemistries such as LCO and LMO and accept the compromise of having a shorter life or a few more safety risks ( considering that it is a small battery), in order to be able to give the product the essential characteristics to be able to enter the market.
Diagrams of this kind are very useful for providing an overview of the characteristics of each chemistry, and these aspects remain true over time. However, we should remember that at quantitative level we are speaking of purely indicative data, due to an important aspect that must never be underestimated: technological evolution.
Both technology and innovation in the broadest sense are constantly evolving concepts and, through them, chemistry also evolves very rapidly and each of them, after the appropriate studies and research, can in turn be developed into other variants to enhance a characteristic rather than another (e.g. to achieve high energy density, perhaps at the detriment of power or life cycle).
This is exactly why it is important to remain constantly up-to-date and, if inexperienced, to rely on an experienced manufacturer which can study and design the battery according to the specific requirements of the application to be electrified.
But chemistry is not the only determining element in defining the correct performance of a lithium battery: battery performance also derives from another important element, the BMS. An intelligent Battery Management System, in fact, can exploit the characteristics of the chosen chemistry to the full, guaranteeing reliability and equal performance over time by managing and controlling all the devices that work around the battery.
We will now learn about the main features of an intelligent BMS.