Battery BMS-Vehicle integration: 5 things to know
25 January 2022
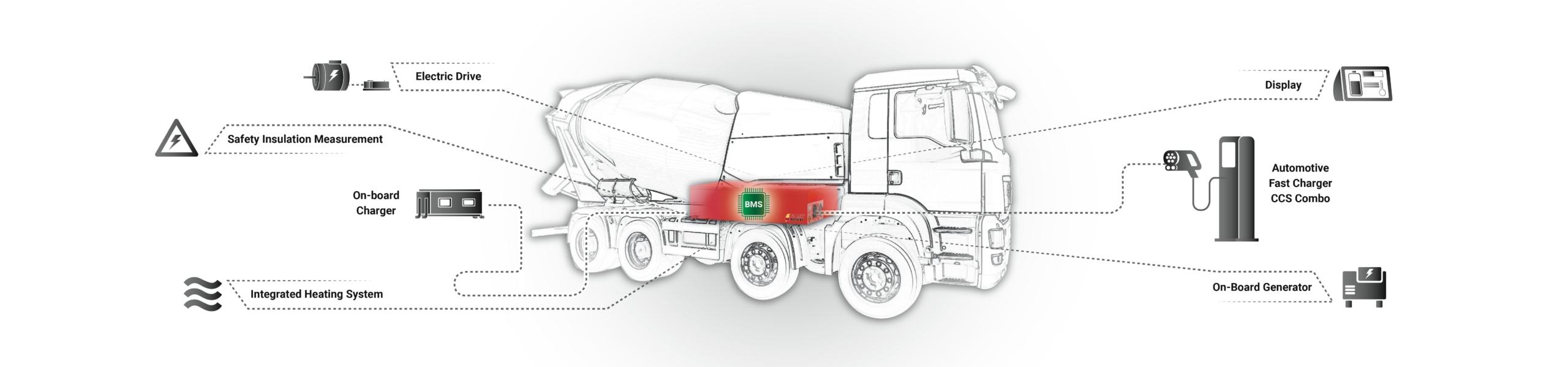
What are the essential characteristics an advanced BMS system (Battery Management System) must have to best do its job as the “brain” of a lithium battery?
You’re in the right place to find out.
We have already extensively covered what balancing is in a lithium battery – one of the essential functions of the BMS system – and how it works. We have also looked at the main differences between the functions of conventional BMS systems and Flash Battery’s proprietary Flash Balancing System.
Read more here: BMS in lithium batteries: what is it and what is its function in cell balancing?
FUNCTIONS OF A BMS SYSTEM
Besides balancing, what are the other 5 functions of a smart BMS system?
Balancing a lithium battery pack correctly is perhaps the most important function of a BMS system. This process is crucial to ensure maximum efficiency and the highest capacity throughout the battery’s entire life cycle.
Flash Battery’s proprietary Flash Balancing System acts both actively and passively with a balancing power that by far exceeds conventional BMS systems (20A), not only at the end of the charging cycle but also in active mode during charging and discharging. This translates into ultra-quick balancing times and maximum run time for Flash Battery lithium batteries.
But there’s more to the Battery Management System. By now widely accepted as the “brain” of a lithium battery, it can manage the safety and range of an electric vehicle by measuring and analysing key functioning data.
If care and meticulous attention is put into its design, it ensures stable performance over time, prevents faults, and performs self-diagnosis and preventive maintenance, providing a comprehensive check of the battery pack.
To recap, the other main functions of a smart BMS system in addition to balancing are:
1. Real time monitoring of every battery parameter
The electronics must be able to check the temperatures and voltage of every single cell in real time, measuring the battery’s incoming and outgoing flow of current. According to the readings, the BMS will take the strategic decisions needed to optimally manage the charge and discharge stages or simply, an extended period of inactivity.
2. Sending information to the vehicle control unit, motor control or on-board display
With lead batteries, the electronics of the vehicle defined the status of the battery, reading only the overall voltage. With lithium batteries, things are different: the battery sends its own data.
Various different data are sent but the most important are:
- the State of Charge (SOC), in other words, the remaining battery level;
- the battery’s life data, Ah drawn from the battery, and life cycles;
- the signals for managing special functions, such as, for example, disabling vehicle functions based on the state of charge or temperature.
3. Controlling the battery charger
In lithium batteries, the battery charger is simply a power supply that delivers the current the battery requires; the charging curve is decided by the battery based on the requirements of each single cell. The CAN bus communication protocol is commonly used to transfer information to and from the battery charger and battery. If, instead, automotive standards are used, such as, for example, CCS Combo charging (the European electric vehicle charging standard), the protocol takes advantage of Power Line Communication.
4. Heating and cooling the lithium battery pack
Depending on the application and the place of use, the battery may be equipped with heating or cooling systems. The BMS system inside the battery activates or deactivates them as required by the battery and vehicle status.
5. Performing predictive analysis throughout the life of the vehicle
In addition to the functions described above, more advanced BMS systems also gather the most significant data, send them to the cloud and analyse them. Flash Data Center, a proprietary platform developed by Flash Battery, analyses every charge and discharge cycle of the interconnected batteries on a daily basis. Using artificial intelligence algorithms, Flash Data Center detects faults before they develop into costly breakdowns by sending automatic alerts to Flash Battery’s service centre.
THE HYBRID CONCRETE MIXER
A Battery Management System to meet the needs of a special electric vehicle: the case of Energya hybrid concrete mixer
We have listed the characteristics for the “standard” operation of a good BMS system in a lithium battery but everyone is well aware that most industrial machines and electric vehicles are special applications with very specific requirements.
That’s why turning to a lithium battery manufacturer that produces the control electronics in-house is crucial. Going to an assembler would mean tremendously lengthening the time to develop the prototype and later, that for servicing when needed.
But let’s talk about a real case:
With the purpose of establishing sustainability as one of the guiding values for the development of its products, CIFA S.p.A., a leading manufacturer of concrete mixer trucks, pump trucks and mixing plants since 2011, chose to rely on the expertise of Flash Battery for the electrification of its vehicles, including the hybrid concrete mixer Energya and the first plug-in hybrid truck pump mixer in the world, the Magnum MK28E.
Both projects required important collaborative work with the customer to develop a battery custom made for the requirements of the application, with high-performance yields, quick-charge capabilities, and high capacity to withstand climatic factors not to mention the mechanical stresses that occur in specialty equipment during daily operation.
Design of a custom BMS system
In addition to the dedicated mechanical part, the Battery Management System was, too, custom made to meet the requirements of the vehicle. The battery, in fact, uses the BMS system to control the on-board battery charger and, at the same time, the charge of a faster, automotive standard charging station at ground.
What’s more, the lithium battery pack communicates back and forth with the vehicle’s control unit, which in turn, sends out the information for the display and the power management of the traction/specific function motors (for example, to operate the mixing drum or pump the concrete). Lastly, the battery controls the generators, the integrated heating system and the insulation measurements, to ensure the safety of the entire vehicle.
“CIFA’s experience and quality led to the decision to use Flash Battery next-gen battery technology and we would like to express our gratitude and pride at having helped create construction vehicles that can offer outstanding efficiency. It is another step forward in sustainable mobility to reduce our environmental impact”.
Marco Righi
Ceo and Founder of Flash Battery – LinkedIn
BMS AND LITHIUM BATTERY
The BMS system: lithium battery’s chemistry first ally
A smart Battery Management System definitely plays a critical role in properly managing the performance and life of a lithium battery, but let’s not forget that its work goes hand in hand with another important ally: chemistry.
A good BMS can definitely make the difference in making the best use of the chosen chemistry, which alone counts for over 70% of the definition of the correct performance of a lithium battery.
Thanks to the BMS system, the chemistry can in fact be improved, ensuring the same reliability and performance over time. This translates into a vehicle with lower losses in terms of state of health and range percentages, maintaining the performance at different temperatures intact because the software is able to manage and control every device revolving around the battery and, if it is well-designed with the hardware part, can help cut down charging times, as is the case for our Flash Balancing System.
Learn more
BMS in lithium batteries: what is it and what is its function in cell balancing?
Our Blog
Would you like to talk to us about your electrification project?