Lithium batteries for Ground Support Equipment: the green revolution promoting airports’ technological transition
24 July 2024
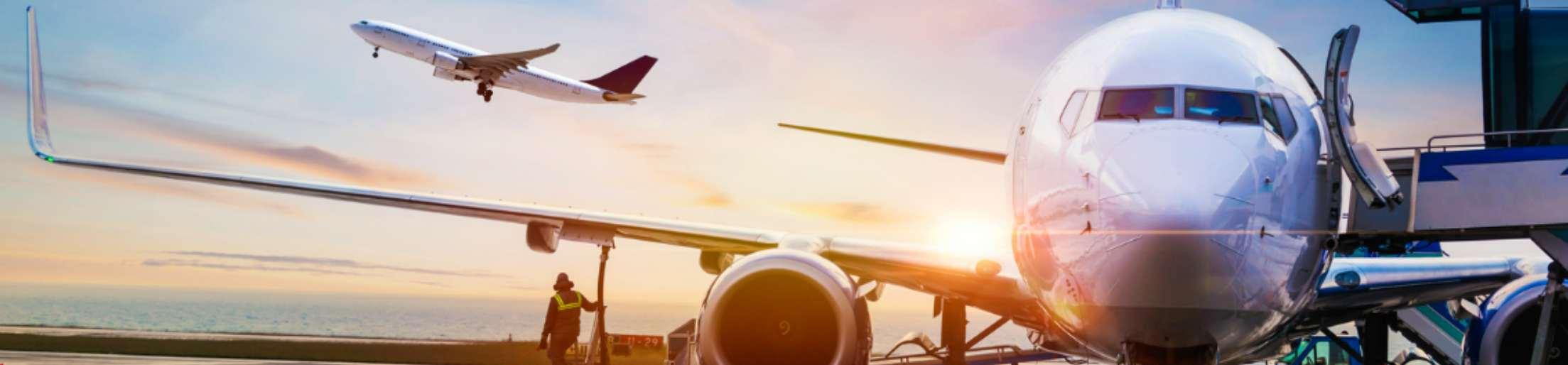
Lowering CO2 emissions and launching a technological transition process at airports has now become a priority for most of the players in this sector, who see the ambitious goals of the European Green Deal not as an obligation, but rather a real lever for increasing the competitiveness of the sector, with the utmost respect for the environment.
Following the setback in 2020 due to the pandemic, the green conversion of airports is now experiencing a major revival: investments are growing and this consequently increases the number of electrified applications. From GPUs up to tow tractors, pushbacks, belt loaders, PRM platforms and boarding stairs, there are many pieces of airport Ground Support Equipment (GSE) that are actively meeting the challenges set by the Green Deal to drastically reduce their emissions by 2030.
Airport electrification
TCO: the key element in electrification choices for Ground Support Equipment
The lowest common denominator in the switch to lithium is the focus on Total Cost of Ownership – TCO, a key parameter for fully understanding the total economic value of an investment.
In fact, while many airport equipment manufacturers were initially put off by the higher purchase price of lithium batteries, field tests and TCO calculations have helped them to analyse the total economic investment and to assess their relative long-term economic benefits, such as the drastic reduction in maintenance costs and energy balance. This calculation shows a clear saving if you choose to follow the path of electrification with lithium batteries.
From lead to lithium with a view to greater efficiency and range
Lead-acid batteries are not just poor in terms of their TCO; this technology is now obsolete and extremely limited in terms of its performance and efficiency, especially from the point of view of its low energy efficiency (75%), high maintenance and infrastructure costs and life-cycle limits, given that, for example, it does not allow fast charging and partial or “opportunity” charging throughout the day. The charging times of lead-acid batteries are also extremely long and require from 6 to 8 hours for a full charge.
The path is now clear: airports, manufacturers and Ground Handlers have fully grasped the advantages of lithium technology compared with its equivalent lead version, starting with its high efficiency at over 96%, fast charging in just 2 hours, long service life (>4000 cycles), zero maintenance and, above all, the possibility of carrying out partial charges and discharges that guarantee a long operating range.
Automatic and predictive maintenance side by side in the Flash Data Center’s latest evolution
Breaks are not an option at airports: everything is dynamic, constantly moving, and machines never stop. This pursuit of speed clashes with the limits set by traditional technologies. In fact, lead-acid electrified or internal combustion machines have two major enemies: the need for maintenance and the possibility of encountering long periods of machine downtime in the event of malfunctions.
If implemented with advanced electronics, lithium batteries can overcome this obstacle, thanks to their capacity to perform predictive analysis throughout the life of the application. Flash Battery was one of the pioneers in the field of predictive maintenance, setting up the Flash Data Center in 2013, a proprietary automated remote monitoring cloud system, whose most recent release uses the latest machine learning and artificial intelligence algorithms to learn, analyse and process operating data 24/7 from all the Flash Battery systems active around the world, nipping any potential critical issues in the bud thanks to predictive maintenance and over-the-air updates.
Let’s look at a real-life example: if in Qatar, an operator leaves a tow tractor out in the sun, at an outdoor temperature of 55°C for a long period of time, the system can automatically send a notification to the Flash Battery after-sales department, which will be able to promptly alert the machine manufacturer and resolve this issue remotely before it can actually cause a malfunction in the battery.
Furthermore, OEMs and Ground Handlers can access the portal on their own, at any time, so they can check the state of health of their batteries, analyse big data on all the active systems on their individual machines around the world, but also perform consumption analysis and specific functions for their entire fleet, so they can study the direction of their future investments as best as possible.