Are we really in the age of “Green Hypocrisy”? Let’s clarify some of the negativity surrounding electric mobility
28 March 2024
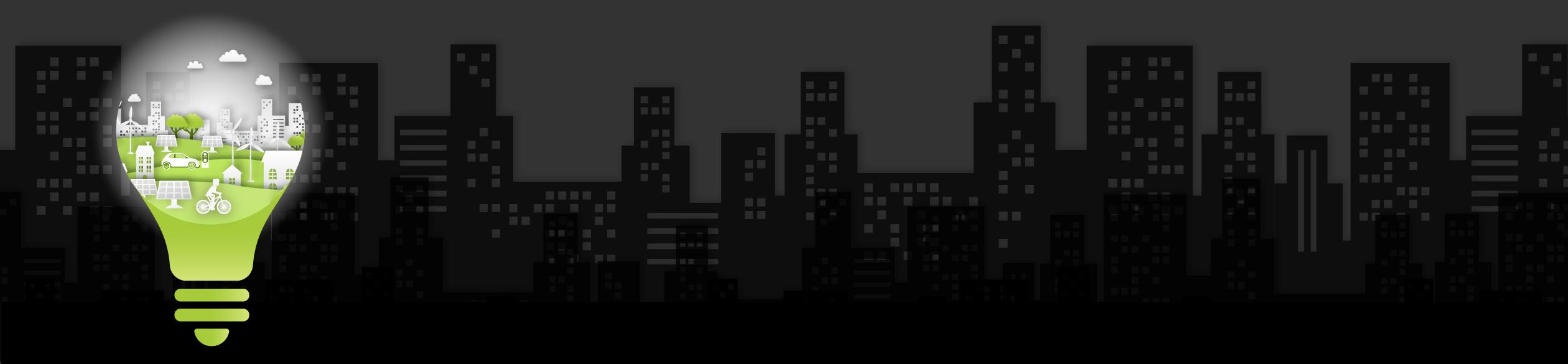
There are certain connections that arise from common interests and shared ideologies which, when fuelled by mutual respect, naturally evolve into trusted relationships. This is the case for our friendship with Silvia Bodoardo, a professor and researcher at the Department of Applied Science and Technology at the Polytechnic University of Turin.
Episode 49 of our Battery Weekly 2023 is one such example of this collaboration, which focused on the subject of electric mobility and the critical issues linked to its roll-out, when we discussed “Green Hypocrisy”, the enquiry by the Italian program Report, aired on 19 November 2023, with Silvia Bodoardo being interviewed in person as a battery sector expert.
Due to the relationship between Flash Battery and Silvia Bodoardo, we felt compelled to shed more light on the subjects addressed during the episode, giving our point of view as manufacturers operating in the lithium battery sector for over twelve years.
The purpose of the “Green Hypocrisy” report was to highlight certain critical issues linked to the world of the green economy, raising important questions about what is going on behind the scenes of the ecological transition, in particular regarding the increasingly widespread adoption of electric mobility. The spotlight was mainly focused on the practices linked to extracting the raw materials used in electric vehicle batteries and the environmental impact these processes have on the land and on people.
In fact, there has always been much debate about the battery sector and, consequently, we need a point of view which, not only analyses its challenges, but can also grasp the opportunities it offers. Mining is certainly a significant subject when it comes to batteries, but it is important not to fall into the trap of sensationalism.
We are responsible for shining the light on its problems and this is an essential step for raising greater awareness, but transparency and comprehensive information must be at the heart of the narrative so we can bring real benefits to society.
However, educational responsibility for what you say must come first: analysis of scientific data and expert opinions are essential to provide information that promotes clarity and transparency, avoiding false scaremongering and encouraging the progress of the entire sector.
It certainly cannot be denied that the increase in battery production has led to huge demand for so-called critical materials. This is supported by recent data that highlights their considerable growth: from 2017 to 2022, overall demand for lithium tripled, while demand for cobalt increased by 70% and 40% for nickel. According to the Announced Pledges Scenario of the International Energy Agency, demand for these materials is forecast to keep growing by 2030.
However, there are certain aspects that must be clarified in order to have a complete and, above all, correct and reliable overview of the role which electric mobility plays in the impact caused by extracting these materials.
We will examine nickel, cobalt and titanium, the three elements covered by the “Green Hypocrisy” report, which blames electric mobility as the main factor responsible for their extraction and any related problems.
Nickel
It is important to point out that only a tiny amount of the nickel extracted is currently used to manufacture electric vehicle batteries. According to data provided by the International Energy Agency (IEA) in its latest annual publication on the electric transport sector, the Global EV Outlook 2023, just 10% of the nickel extracted was used for electric vehicle batteries in 2023.
So where does the remaining nickel extracted end up?
Its main use, accounting for over 70%, is in the metalworking industry for the production of stainless steel. This widespread material is a common iron-based alloy which is used in various sectors, from food to construction. We also have to remember that objects smaller than an electric car but found almost everywhere, such as smartphones, tablets and notebooks, still contain nickel.
While the nickel extraction process in Indonesia is notoriously associated with a substantial social and environmental impact, we then have to remember that this material is used in a wide range of production sectors. Rather than pointing the finger at the battery industry, which only accounts for a small part of its total use, it would be better to think about how we can all work together to limit its use on a large scale or reduce the impact of its extraction.
*[Fig1]
Representative graph of Nickel production and demand by sector, 2016 – 2022
Titanium
The Report then moves on to titanium and more specifically to titanium dioxide. Once again here, it is important to underline that titanium dioxide, known as TiO2, is currently used in various industries, including paints, paper, cosmetics (for example, in the production of sun cream and toothpaste), pharmaceuticals and ceramics.
While in the automotive industry, TiO2 is widely used as a white pigment in external coatings to reflect sunlight, reducing the heat inside the vehicle and therefore the need for energy for air-conditioning. Certain titanium dioxide coatings are also photocatalytic, which means that they can reduce air pollution through the decomposition of pollutants, such as nitrogen oxides when exposed to sunlight.
Another use for titanium dioxide in electric vehicles is inside air filters to improve the air quality inside the vehicle passenger compartment, therefore reducing the presence of harmful substances.
We can therefore say that titanium dioxide has various applications, but it is not directly involved in powering electric vehicles, which therefore means that its use in this field is still limited.
Cobalt
Finally, we look at cobalt, a metal closely linked to electric mobility, which has a big impact on the environment, as the TV programme quite rightly emphasised.
Unlike many other metals, cobalt is not found in its pure state, but as a mineral, and is extracted as a by-product in the extraction of copper or nickel. Cobalt has various applications in industry, for example as a colouring or additive, but it is in lithium batteries that it plays a particularly important role. It is used here in the form of cobalt hydroxide inside the cathode, or in the negative pole, thanks to its thermal stability and high energy density.
*[Fig2]
Representative graph of Cobalt production and demand by sector, 2016 – 2022
Cobalt has been the subject of growing attention over time due to its extraction conditions, which are often associated with ethically questionable situations. In particular, most cobalt is extracted in the Democratic Republic of Congo, a country blighted by armed conflict as well as social and political instability.
Companies that are seeking to cut the social risks and costs of battery production have actually been trying to reduce the cobalt content for decades. To tackle this problem, various businesses in the lithium battery sector have launched initiatives to improve cobalt extraction conditions or to develop cobalt-free alternatives.
This commitment has resulted in major developments in the sector from 2019 to date. According to IEA data, a major change has occurred in recent years in the chemistries used for the production of cathodes. In fact, nickel manganese cobalt-based chemistries (NMC) have evolved over time towards solutions with a lower and lower cobalt content.
LFP chemistry: a viable alternative
However, the “Green Hypocrisy” report overlooks the fact that there are already several batteries that do not contain nickel or cobalt: this is the case with LFP batteries, or lithium-iron-phosphate, which have experienced a real boom in recent years.
According to IEA data, in 2022, NMC batteries accounted for 60% of the end market, followed by lithium-iron-phosphate (LFP) with a share of just under 30%, proving how much LFP chemistry is taking on an increasingly significant role on the market. Current forecasts predict it will continue to grow over the next few years.
So, while NMC batteries have dominated the electric vehicle market for years, the growing roll-out of LFP batteries is reshaping the battery technology scene.
What are the reasons behind the incredibly swift roll-out of LFP chemistry?
- The rise of LFP chemistry undoubtedly comes down to the lower amount of critical raw materials used in it. In fact, this chemistry does not contain any nickel, manganese or cobalt, alleviating concerns regarding the stocks of these materials, whose supply chains are more concentrated into the same geographical areas and subject to disruption.
- LFP batteries are also considered safer as they are less susceptible to issues such as overheating and fires, thanks to their greater thermal stability, a feature that makes them particularly suitable for use in electric vehicles.
- LFP batteries are generally cheaper to make than NMC ones, primarily due to the lower amount of precious metals required to make them, particularly nickel and cobalt.
- LFP batteries are known for their longer life over time and for their capacity to keep performing well even after a high number of charge/discharge cycles.
Even though their energy density tends to be lower than NMC and NCA chemistries, with their benefits in terms of safety, cost, duration and environmental sustainability, LFP batteries are emerging as an increasingly popular choice among electric vehicle manufacturers.
In fact, many car manufacturers have invested in this technology, starting with China right up to closer to home in Europe. One such example is the initiative by Volkswagen to produce entry-level models in Europe with LFP batteries as well as Ford’s decision to build an LFP battery production plant in the United States.
Just criticising the current limits of electric mobility, without objectively looking at the many steps which Europe is taking towards ever greater transparency and sustainability, would only provide a partial, incomplete overview of the current state of the sector.
European batteries are created to be sustainable and recyclable and our continent is taking many steps in this direction to organise a production chain that has a lower and lower environmental impact in the long term and to guarantee a safer, more sustainable supply chain. This commitment is reflected both in regulations aimed at promoting transparency and responsibility all throughout the battery production chain, and in the efforts to develop innovative solutions for recycling batteries.
The Critical Raw Materials Act to guarantee safe and sustainable supply chains
In terms of legislation, the European Union has brought in regulations aimed at ensuring that the materials used in the production of lithium batteries are ethically and sustainably extracted, therefore reducing the risk of exploitation and violations of human rights in mining regions.
In 2023, this commitment resulted in the drafting of the Critical Raw Materials Act. Europe adopted this regulation in order to diversify sources of supply, reducing its dependency on third countries and promoting safe access to these materials.
Through this document, the European Union committed to identifying and monitoring any essential critical materials for the European economy, assessing the risks associated with their availability and production and promoting policies aimed at guaranteeing sustainable management of resources and at encouraging technological innovations to reduce its dependency on critical materials and to develop more sustainable alternatives.
*[Fig.3]
These ambitious goals take shape in concrete initiatives, such as research and development programmes to identify alternatives to critical materials, international cooperation initiatives to guarantee responsible sourcing and investment policies to promote the sustainable production and recycling of these materials across Europe, in line with industry’s sustainability goals and targets to reduce its environmental impact.
Meanwhile, the European Union is investing in advanced technologies for battery recycling, in order to recover and reuse precious materials such as lithium, cobalt and nickel, therefore reducing its dependency on virgin raw materials and mitigating the environmental impact linked to extraction and the production of new batteries. These materials can be extracted from used batteries and reused in the production of new batteries or in other industrial sectors, helping reduce demand for virgin raw materials and minimise the environmental cost associated with their extraction.
The lithium used in batteries does not disappear into nothing once the battery’s life-cycle is over: it stays inside the used battery and can be recovered through recycling processes.
As proof of this, already back in 2021, the Norwegian battery manufacturer, Northvolt, ran production tests using 100% recycled material, therefore making the first NMC battery entirely out of recycled material. This initial experiment, which is part of the Norwegian company’s recycling programme called Revolt, proved that it is possible to achieve comparable performances between cells made with recycled material and cells made with virgin material.
Unlike oil, which must be continuously extracted to power petrol cars, lithium is only extracted once for the production of batteries. In fact, we should consider that lithium, cobalt, manganese, nickel and all the other materials in a battery pack can be recycled and reused several times. However, there is currently a lack of raw materials being recycled, given that it is only in the last few years that we have started to add significant volumes of batteries onto the market, which have an average lifespan of about 15-20 years. This is therefore an essential issue that needs to be addressed in the long term.
It is a similar concept to the one we already experienced in the lead sector, where we managed to turn what was once a manual mining process into a well-established recycling system. Today, the lion’s share of the lead used is obtained through recycling, but this change did not happen overnight: time was needed to develop the necessary infrastructures and technologies.
After 4 seasons, 150 recorded episodes and dozens of well-known guests, we have learned one thing for certain from our Battery Weekly: innovation in the battery sector moves fast and there is a constant flurry of activity in research.
The world of chemistry applied to batteries is rapidly evolving, not just in the adoption of more advanced technologies, but also in the exploration of new, increasingly different chemistries with the goal of ever greater sustainability. Significant progress has been made in the research and development of new chemistries aimed at reducing or eliminating the use of materials seen as critical or harmful to the environment and human health: one such example is sodium technology which is already making its first steps on the battery scene, with growing interest.
To tackle these challenges, we need major investment in research and development for sustainable and advanced recycling technologies, as well as in the creation of appropriate regulations and infrastructures to support the recycling of batteries on a large scale. However, all this is not enough if it is not supported by accurate and objective communication, aimed at raising awareness and actively engaging the public in an open and transparent dialogue, clarifying rather than confusing things and educating rather than scaring people.
Notes*
Source Fig. 1: Overall supply and demand of battery metals by sector, 2016-2022. Picture taken from Global EV Outlook 2023 by the International Energy Agency. https://bit.ly/4auvUfN
Source Fig. 2: Overall supply and demand of battery metals by sector, 2016-2022. Picture taken from Global EV Outlook 2023 by the International Energy Agency. https://bit.ly/4auvUfN
Source Fig. 3: Critical Raw Materials act. Picture taken from European Commission website on 20/03/24. https://bit.ly/43BGnDM