Next-Generation Batteries: Progress and Future Directions
18 December 2024
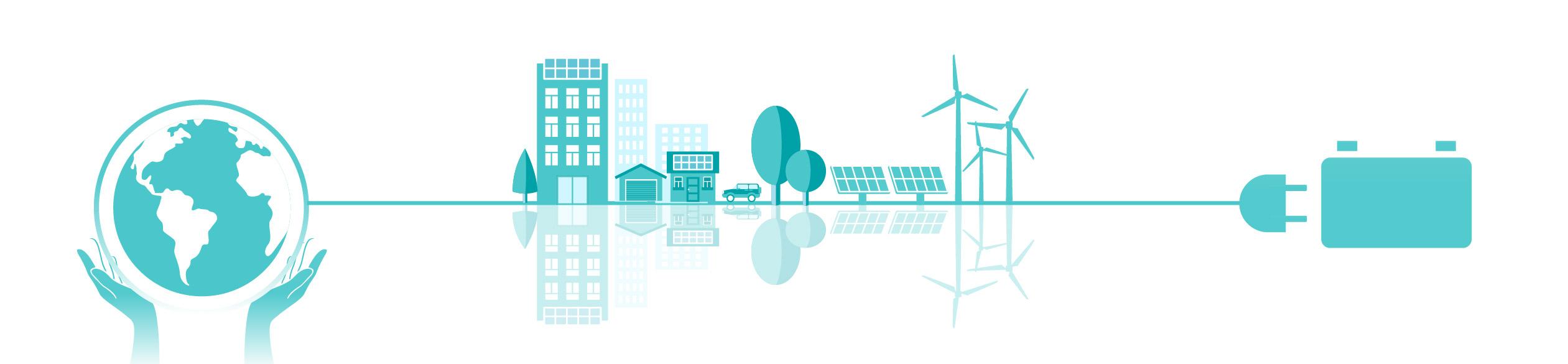
More than three decades after their invention and subsequent commercialisation, lithium batteries have dramatically reshaped modern mobility. Now, we stand on the brink of a new era, poised to transform the future of energy storage with next-generation batteries. Europe’s Green Deal sets an ambitious target for a climate-neutral society, advocating for the gradual electrification of sectors currently reliant on fossil fuels. In this endeavour, batteries emerge as crucial allies.
There is a growing imperative to invest in research and development. The goal is to advance existing technologies to meet market demands and cater to the needs of increasingly diverse sectors.
Rather than replace current technologies, these advancements will expand the range of possibilities. By enhancing the technological landscape, these innovations will unlock their potential in various applications and support the diversification of raw material supplies.
European Roadmaps
European Roadmaps: Charting the Future of Battery Innovation in Europe
In any major project, having a clear roadmap that outlines the path and objectives is essential.
At the European level, various Battery Roadmaps, such as Battery 2030+ and Eurobat, have been created to steer the future of research and innovation in new chemistries and more sustainable, efficient materials for battery cells. These collaborative projects are pivotal in strengthening Europe’s market position. Through targeted research actions, they aim to revolutionise the development and design of ultra-high-performance batteries that are both sustainable and practical for real-world applications.
Currently, Europe lags behind Asian countries in this field. To compete globally, it must close the existing technological gap. Recent supply chain interruptions, raw material cost increases and the need to secure critical raw materials have underscored the importance of diversifying the development of advanced technologies for specific use cases.
The objectives of the European Battery 2030+ roadmap
The Objectives for Next-Generation Batteries
High Energy Density, Enhanced Safety and Greater Sustainability: These are the Objectives for Next-Generation Batteries
The batteries of the future must address clear priorities, with the main goal being the maximisation of battery performance while also aiming for cost reductions and high safety standards.
Alongside the pursuit of greater energy density, cost-effectiveness and longevity, sustainability will be a critical factor. The aim is to ensure that the chosen materials not only meet immediate performance requirements but also align with long-term sustainability goals, minimising any potential environmental or recycling challenges that could arise as these materials are gradually adopted by the market.
This effort focuses on developing different chemistries with a clear feasibility outlook in terms of the scalability of production processes. In this context, TRL (Technology Readiness Level) is a vital indicator to gauge how close a technology is to mass production. It is an assessment methodology that indicates a technology’s state of evolution and maturity, essentially how ready it is for commercialisation. While technologies with a high TRL, such as LiFePO4 (LFP) and NMC, are already well-integrated into industrial processes, those with a lower TRL are still in the R&D phase.
The State of the Art of Today’s Batteries
The State of the Art of Today’s Batteries: Which Generation Are We Currently at?
We are currently in Generation 3 of battery technologies, specifically in the phase known as Generation 3a. Although some battery systems on the market qualify as “Generation 3”, their performance still falls short of the expectations set for 2030.
The industry is primarily focused on optimising the current NMC and LFP chemistries, aiming to balance energy density, costs and sustainability. Efforts include reducing cobalt content, incorporating silicon anodes and minimising the use of critical materials. Simultaneously, the attention is shifting towards next-generation batteries with the promise of a better balance between high performance, safety and reduced environmental impact.
Generation 3b, initially considered the next step in improving energy density, remains in its early stages and is not yet ready for implementation. This is also due to the cost, performance and production effort required to develop the samples.
The Two Chemistries the Market Is Focusing on Today: LiFePO4 and NMC
Cell production, particularly in the mass market, is primarily focused on two key technologies: LiFePO4 (LFP) and NMC, each addressing specific application needs.
LiFePO4 (LFP, lithium-iron-phosphate) chemistry is capturing a growing market share due to its safety, sustainability and long life cycle, making it a popular choice for applications that require a good cost-performance balance.
The use of LFP batteries is also evolving in the automotive industry, which increasingly views this chemistry as a solid technology for vehicles, offering high safety and lower raw material costs. Notable names like Tesla and BYD have already integrated LFP batteries into their range, and manufacturers like Ford and Renault have announced plans to start using them soon.
NMC (nickel-manganese-cobalt) chemistry remains a top choice in the high-performance automotive world, thanks to its very high energy density and capacity to deliver significant power. However, these batteries have a shorter life cycle than LFP batteries and a greater environmental impact due to the cobalt content.
Research in this area is heavily focused on reducing the percentage of this crucial and costly component. This has led to the development of the NMC111 chemistry, with a composition of nickel, manganese and cobalt in equal proportions, and more recent iterations like the NMC622 chemistry (60% nickel, 20% manganese, 20% cobalt) and the NMC811 chemistry, which has a significantly reduced amount of cobalt (10%) and nickel in greater proportions (80%).
Outlook
Outlook: The Evolution of Lithium-Based Chemistries
Lithium-based chemistries have a well-defined evolutionary roadmap, with ambitious objectives and significant technological developments on the horizon. These advancements make them a key resource to watch for the future. Due to their versatility and high performance, these chemistries will remain a cornerstone for developing new applications.
Research Focused on Solid Electrolytes and Silicon Anodes
Several European collaborative projects are aiming to develop fourth-generation lithium-ion batteries with solid electrolytes, with or without lithium-metal anodes, as a long-term industry solution.
The introduction of silicon anodes could also mark a significant step forward. While, currently, lithium batteries on the market primarily use graphite anodes, future research aims to combine traditional graphite anodes with a percentage of silicon.
Solid-state batteries with lithium metal could potentially reach energy densities twice as high as current ones.
Furthermore, recent industrial studies have highlighted the promising potential of LMFP (lithium-manganese-iron-phosphate). This variation of LFP chemistry increases the concentration of manganese in the cathode material to 80%, compared to the traditional values of 50% to 70%.
This configuration maintains the distinctive safety level of LFP batteries while increasing battery life by 20%.
Post-Lithium-Ion Chemistries: Promising but Need More Time for Development
While lithium-ion batteries are a well-established technology, research is already looking ahead, pioneering breakthroughs that go beyond present limitations. These chemistries, known as post-lithium-ion, exist but are not yet produced on a large scale.
Among these are all-solid-state batteries (Li-ASSB) with lithium-metal anodes, which are not to be confused with other solid state batteries (described below). These promise significant advantages in terms of efficiency and safety. Although not fully adopted for traction, these solutions are already used in devices such as smartphones and drones.
Looking further ahead, technological roadmaps contemplate the introduction of lithium-air chemistry, a solution that would exploit the reaction between lithium metal and oxygen in the air. This approach could significantly increase the battery’s energy density and performance. However, it remains a distant possibility, requiring further study and experimentation before becoming a concrete reality.
Sodium: A Viable Alternative
Sodium: A Viable Alternative for Applications Not Requiring High Performance
Expected to enter the market after 2025, sodium batteries, while unable to match lithium’s performance in terms of power and energy density, could nevertheless offer a cheaper alternative. Although they cannot equal lithium’s energy density, sodium batteries could become competitive in terms of life cycle longevity with further research and development. Their lower costs and reduced energy density would make them suitable for applications such as stationary solutions or entry-level electric vehicles with limited range.
Currently, the volumetric density of sodium batteries is about half that of LFP chemistry. Since they are not yet produced on a large scale, the current costs of sodium batteries still exceed those of LFP batteries, making economic competitiveness difficult for now
Solid State
Solid State: Prospects for Enhanced Safety
In the realm of fourth-generation cells, solid-state batteries stand out as a key innovation, garnering increasing interest.
Their most significant advancement lies in the use of a solid separator instead of liquid electrolyte. Firstly, removing the liquid electrolyte enhances safety, almost completely eliminating the risk of fire.
Secondly, this technology, combined with the use of pure lithium anodes, offers tremendous potential for significantly increasing energy density, despite some challenges in this configuration. Solid-state batteries with lithium anodes are currently the focus of extensive studies and technological developments.
Next-Generation Batteries
Creating Next-Generation Batteries: A European Opportunity
The design of next-generation cells not only affects the characteristics of the batteries themselves but also has a ripple effect on the entire supply chain, from raw material extraction to recycling. An increase in performance and energy density at the cell level could significantly boost the sector’s overall efficiency while ensuring Europe’s global technological leadership.
Europe has the potential to regain lost ground in battery sector competence development, but a step-up is required to compete against Asian-based actors. These competitors, with their higher production volumes and significant investments in innovation, are pushing the boundaries of both technology and the industrial processes related to batteries. Currently, Europe faces clear challenges: recent battery gigafactory developments indicate that the industrial ecosystem is still not prepared to rival Asian giants.
However, Europe could emerge as a leader in battery recycling. This sector represents a strategic opportunity, supported by a strong research and innovation community that is already demonstrating its ability to develop advanced recycling technologies for critical materials.
“To advance the development of next-generation batteries in Europe, it is increasingly vital for Europe to invest in cutting-edge technologies that allow for the simulation of battery behaviour and predictive analyses, such as digital twins. The integration of smart functionalities, to continuously monitor state of health and safety and perform predictive maintenance, will be central to developing safer, more efficient and durable batteries. Recycling can become a competitive advantage, reducing reliance on imported raw materials and contributing to greater sustainability in the sector”.
Alan Pastorelli
CTO of Flash Battery – LinkedIn
Discover
Why the Flash Battery lithium batteries are a different breed from the competition ones ?
Our Blog
Would you like to talk to us about your electrification project?