Lithium battery transport: all you need to know
20 December 2022
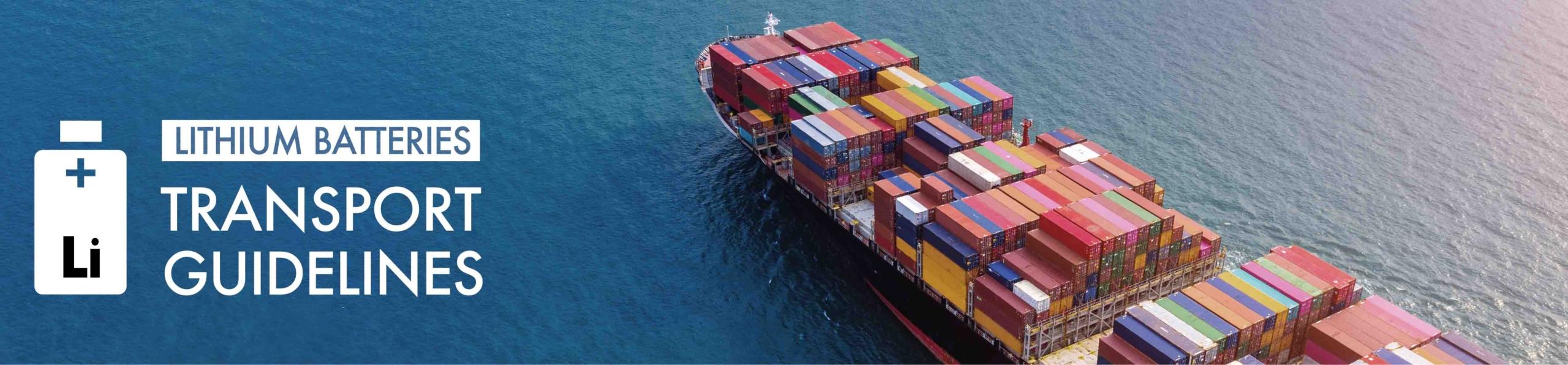
The ever-increasing demand for lithium batteries has led to the introduction of legislation and regulations to manage their transport more effectively.
These days we live in a world in which energy drives almost all human activities. From agriculture and heavy industry to services and “personal technology”, no sector can claim to be exempt from this constant demand.
Also part of this phenomenon is the industrial electrification sector, which, driven by increasingly pressing international sustainability policies and the considerable benefits of the energy transition, is experiencing a particularly prolific period.
In recent years, the word “electrification” has most been often associated with lithium batteries.
While they initially involved computers and small tooling applications, lithium batteries have gradually evolved towards the electrification of hybrid or full-electric vehicles and today more and more manufacturers of industrial machines and electric vehicles are turning to this technology for the electric transition of their fleets and/or plants.
The sharp increase in demand has resulted in the need to “secure the arrival” of these products to global markets, which has led to an impressive increase in flows, thus necessitating the introduction of legislation and regulations to manage lithium battery transport more effectively.
However, when it comes to lithium batteries, the subject of safety attracts the attention of users and is an issue that affects all stages of the supply chain, transport included.
Nowadays, different lithium-based chemistries are available on the market, each with its own particularities and characteristics, making them more or less suitable for any given application. Chemistry is not the only determining element when it comes to defining the correct performance of a lithium battery: such performance also derives from another important element – the Battery Management System (BMS).
Indeed, a BMS is capable of making the most of the characteristics of the chosen chemistry, ensuring reliability and equal performance over time by managing and controlling all the devices that revolve around the battery.
C-Rate, thermal stability and specific energy are some of the characteristics related to the thermal risk of batteries, or to chemical, electrical and kinetic risks.
For these reasons, lithium batteries are classified as dangerous goods, in the same manner as chemicals or flammable goods. Like any other material, they can be transported in all modes, such as by road, sea, rail or air.
Nevertheless, as they are part of the list of dangerous goods, their transport is subject to specific regulations to ensure their proper handling and protection throughout the haulage and storage phase, in order to avoid unpleasant situations, such as fires. It is precisely for this reason that they are classified as “dangerous goods” and that their handling, both domestically and internationally, is subject to special European regulations, as well as to a special type of packaging for shipment.
What are the “rules” to be followed and how can lithium batteries be transported safely?
- RID: Regulation concerning the International Carriage of Dangerous Goods by Rail
- ADR: European Agreement concerning the International Carriage of Dangerous Goods by Road
- ADN: European Agreement concerning the International Carriage of Dangerous Goods by Inland Waterways
- IMDG: International Maritime Dangerous Goods Code
- IATA DGR: International Air Transport Association Dangerous Goods Regulations
Each regulation gives the requirements for the safe transport of such dangerous goods and indicates the obligations and responsibilities to be fulfilled by all parties involved. Each of these standards also furnishes information on the criteria for classifying goods, the most appropriate packaging, the conditions for transport, the marking of packages and transport units, the drafting of transport documentation and the types of vehicles deemed suitable.
The classification of batteries for transport
Lithium batteries, like all objects classified as “dangerous”, are associated with a specific hazard class. Lithium ion batteries are in fact Class 9: Miscellaneous – Hazardous Materials. This implies that all shipments of such goods are required to carry the specific label for this class.
To ensure complete transport safety, lithium batteries are divided into two categories under legislation:
- Rechargeable batteries (usually lithium ion)
- Non-rechargeable or disposable batteries
A second distinction takes into account the method of packaging with which they will be shipped:
- Battery alone
- Battery with a device (car, vehicle or generic device)
- Inserted inside the device itself
UN codes identifying the type of goods
Once the nature of the material to be transported and the characteristics of the consignment have been defined, it will then be possible to identify the UN code number (consisting of 4 digits preceding the abbreviation “UN”), assigned by the international UNECE committee, in order to identify unambiguously and globally a particular type of dangerous item.
For rechargeable lithium ion batteries, the assigned codes are UN3480 and UN3481.
Class 9 – UN3480 – Lithium ion batteries – Batteries that are not packed with or installed with the equipment.
This UN code identifies lithium ion batteries packed without the device, i.e. those batteries that are shipped separate from the devices with which they will be used by the end customer.
In Flash Battery, for example, lithium batteries are shipped under the code UN3480.
Class 9 – UN3481 – Lithium ion batteries contained in or packed with the equipment, but not attached to the source.
Conversely, batteries contained within equipment, and which arrive at their destination already installed in the equipment or device for which they were designed, are classified with the above code.
This classification applies both to lithium batteries packed together with the equipment or device for which they are designed, but not directly installed or connected, and to batteries already installed and connected to the instruments that will use them.
Additional battery requirements to be communicated to carriers
Once the type of classification to which the specific lithium battery belongs has been precisely identified (UN3480 or UN3481 – not forgetting that the correct classification can also be easily found via the Material Safety Data Sheet – MSDS), it is also necessary to provide further information for which there may be specific requirements: battery weight, size, capacity and state.
The “state of the battery” item is of paramount importance in order to be certain that you have used the correct packaging and do not receive complaints from transporters.
Battery states can be subdivided into the following cases:
- New batteries
- Defective or non-working batteries (not damaged)
- Batteries for disposal or recycling
- Seriously damaged batteries (as a result of an accident or test)
- Prototype batteries or small production batches of less than 100 pieces
In the case of batteries that are declared damaged, special packaging may be required by transport authorities to ensure the safety and protection of those transporting them.