Lithiumbatterien für Baumaschinen: auch Baustellen werden jetzt elektrifiziert
22 Oktober 2024
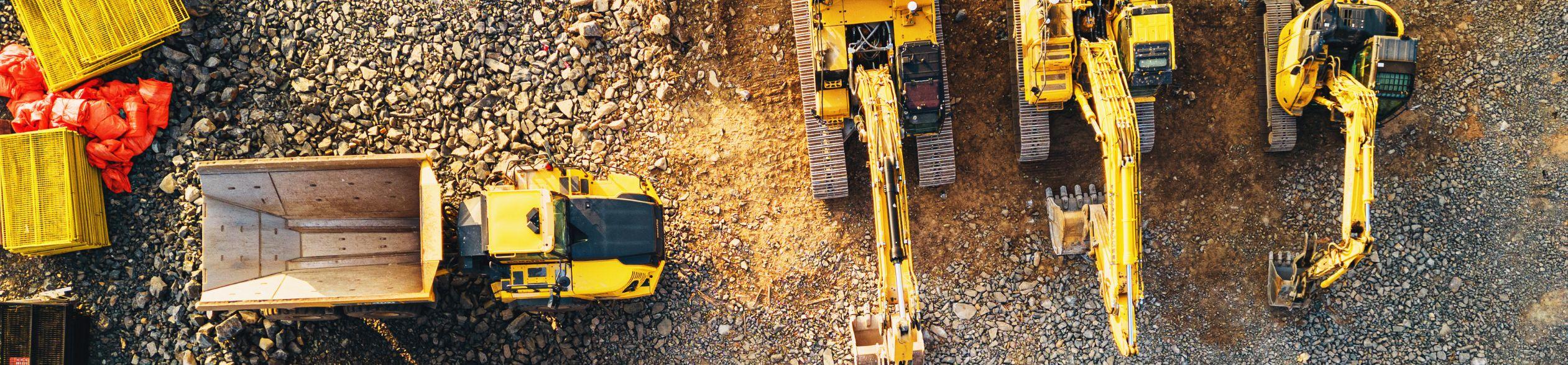
Die Umstellung auf elektrische Baumaschinen ist schon seit einiger Zeit im Gange. Hauptziel ist hierbei, die Treibhausgasemissionen drastisch zu reduzieren und die ehrgeizigen Ziele des Pariser Abkommens zu erreichen. Ein Prozess, von dem zunächst kompaktere Maschinen betroffen waren, der sich aber allmählich auch auf leistungsstärkere und größere Maschinen und Fahrzeuge ausweitet.
Und wenn sich das Bauwesen, einer der Industriezweige, der weltweit schon immer ein großer Produzent von Emissionen war, für die Elektrifizierung entschieden hat, dann stellt sich eine Frage: An welchem Punkt befindet sich die technologische Entwicklung der Lithiumbatterien und wie können sie den Anforderungen dieser energieintensiven Fahrzeuge und Maschinen gerecht werden?
Während bis vor kurzem die NMC-Technologie aufgrund ihrer Fähigkeit, eine sehr hohe spezifische Energie (220-240 Wh/kg) zu liefern, bei der Elektrifizierung von Baumaschinen dominierte, nimmt heute die LFP-Technologie einen immer wichtigeren Platz ein. Sie bietet vor allem eine erhöhte Energiedichte von bis zu 190 Wh/kg, zu der ein weiterer, von der Industrie besonders geschätzten Aspekt hinzukommt: die Sicherheit.
Sicherheit der Batterien: eine Priorität auf der Baustelle
Der Zugang zu Technologien, die die Sicherheit der Baustelle erhöhen, ist heute ein strategischer Hebel bei den Kaufentscheidungen aller OEMs und Hersteller, die in die Elektrifizierung ihrer Flotten investieren wollen.
Dank ihrer hohen Zersetzungstemperatur und der langsamen Wärmeabgabe – zwei Aspekte, die ein thermisches Durchgehen in kritischen Situationen verhindern – sind Lithiumbatterien mit LFP-Technologie auch in der Baubranche eine ausgezeichnete Wahl.
Diese Technologie ist in Verbindung mit einer ordnungsgemäßen Zellmontage und intelligenten Steuerelektronik, wie dem Flash Balancing System von Flash Battery, der ideale Kompromiss zwischen Energie und Zuverlässigkeit.
Die Entscheidung für eine Batterie, die etwas mehr Platz benötigt, aber hohe Leistung und optimale Sicherheit gewährleistet, ist in der Tat geschickter, insbesondere bei den immer beliebter werdenden Hochspannungssystemen, die 800 V überschreiten können und die, wenn sie nicht sorgfältig ausgelegt sind, eine echte Gefahr für den Bediener darstellen können.
Null Emissionen für maximale Betriebseffizienz
Der Wettlauf um die Senkung der Schadstoffemissionen von Fahrzeugen mit Verbrennungsmotoren ist nicht nur eine Folge der jüngsten europäischen Vorschriften zur Dekarbonisierung: Der Einsatz elektrischer Maschinen ermöglicht nicht nur eine drastische Verringerung (wenn man sich für Hybridfahrzeuge entscheidet) oder eine vollständige Eliminierung (wenn man sich für vollelektrische Fahrzeuge entscheidet) der CO2-Emissionen, sondern auch eine Optimierung der Arbeitszyklen, da die Baumaschinen auch über lange Zeiträume in geschlossenen Räumen arbeiten können, ohne dass eine Unterbrechung erforderlich ist, um die von den Verbrennungsmotoren erzeugten giftigen Gase abzuführen.
Ein weiterer konkreter Vorteil von Lithiumbatterien in dieser Branche ist die geringere Geräuschentwicklung. Und es ist die Vermeidung von Geräuschemissionen, die für große Flexibilität bei der Nutzung in städtischen Gebieten sorgt, wo die Fahrzeuge ungestört und ohne zeitliche Beschränkungen arbeiten können.
Die Umstellung vom Verbrennungsmotor auf einen Elektromotor begann zunächst bei Anwendungen mit weniger als 50 kWh, heute erobert die Elektrifizierung auch den Bereich der leistungsstärkeren und größeren Maschinen und Fahrzeuge. Grund hierfür ist die sich ständig weiterentwickelnde Lithiumtechnologie, die immer mehr Energie auf kleinem Raum speichern kann, um die typischen Arbeitszyklen von Baumaschinen bewältigen zu können.
Angesichts der Situation und der Kenndaten der derzeit genutzten Technologie in Bezug auf Energie, Volumen und Ladeinfrastruktur bringt die Umstellung schwerer Fahrzeuge, z. B. großer Bagger, auf eine 100 % elektrische Lösung jedoch eine Reihe großer Herausforderungen mit sich und bleibt vorerst noch ein Zukunftsprojekt.
Bei diesen Fahrzeugen, die einen sehr hohen Energiebedarf haben und belastungsintensiven Arbeitszyklen ausgesetzt sind, ist ein Hybridsystem, bei dem die Batterie für einige Stunden genutzt und von einem Generator unterstützt wird, um die Stromversorgung weiterhin zu gewährleisten, sinnvoller.
Heute sprechen wir in diesem Zusammenhang noch von Dieselgeneratoren, in naher Zukunft könnten es jedoch mit Wasserstoff betriebene Brennstoffzellen, sein, eine Technologie mit großem Potenzial, die sich jedoch noch in der Entwicklung befindet.
Der Dekarbonisierung wurde folglich bereits auch bei den großen und schweren Maschinen in Angriff genommen, ist jedoch noch mit einigen Herausforderungen verbunden, angefangen bei der fehlenden Ladeinfrastruktur und den Schwierigkeiten, die anspruchsvollen Arbeitszyklen auf Energieseite ausreichend zu unterstützen.