Discover remote monitoring software that improves the performance of lithium batteries: the evolution of Flash Data Center
27 September 2022
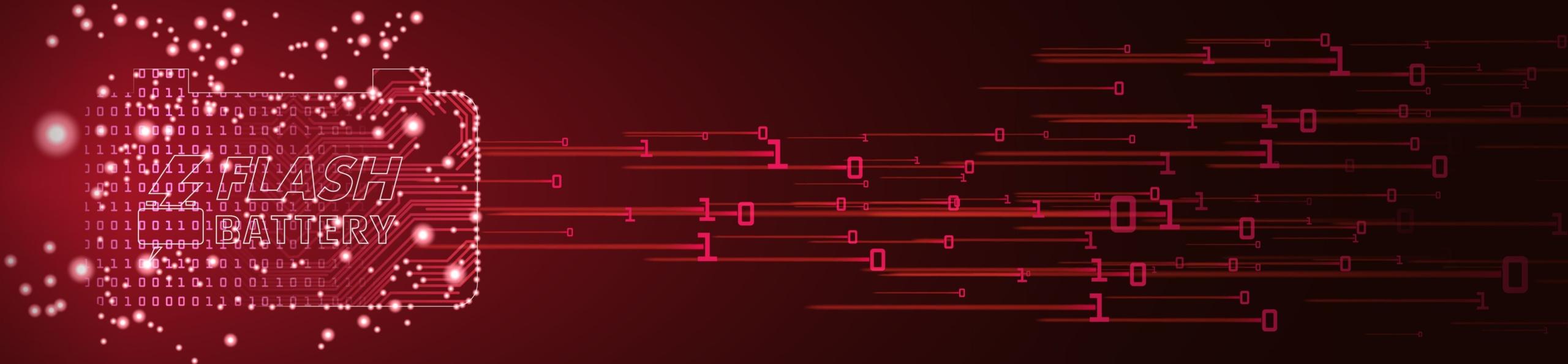
We are in the midst of the era of digitalisation, surrounded by apparently limitless technology. Terms such as IoT, Machine Learning and Artificial Intelligence are part of our everyday lives, guaranteeing us speed, interconnection and increasingly diversified communication.
But have we ever really asked ourselves how this is all possible? If artificial intelligence is set to become a pillar of digital transformation in the most diverse sectors of the world economy, this is possible thanks to a multitude of people who have invested their time in research and innovation.
Ten years ago, when we decided to produce lithium batteries for industrial machinery, we did so by looking in this very direction, choosing not to stop at simple battery design, but developing what was to become Flash Data Center, the automatic remote monitoring software able to run self-diagnostic tests and predictive analysis of lithium batteries.
Flash Data Center is proprietary remote monitoring software designed and implemented back in 2013 to monitor, on a daily basis, how each lithium battery we’ve ever sold is being used, regardless of where it is in the world.
A genuine pioneer in the field of remote monitoring, its main function is the automatic monitoring of data in real time: the software monitors and analyses, 24/7, the data received on the performance of all active Flash Battery lithium batteries and sends this information both to the client and to the technical assistance department. This indispensable tool is a powerful self-diagnostic and predictive maintenance system that helps to stop misleading reports and anomalies before they gain traction and to prevent faults.
Further development of the remote monitoring of batteries with the latest release of Flash Data Center
The latest version of Flash Data Center 4.0 was ranked among the 41 finalists for the Bauma Innovation Award 2022, the prestigious international award for the best industrial projects in the area of research and innovation.
What makes it special?
From today, Flash Data Center is also integrated into a virtual environment with Containerized Architecture, harnessing the power of latest-generation artificial intelligence and machine learning technologies to ensure the interconnection of the over 25,000 Flash Battery systems currently operating in 54 countries across the world. It is a true system that learns from the data analysed and improves battery performance.
In this way, OEMs and producers that rely on Flash Battery technology can perform advanced analysis of the big data coming from their battery systems in real time. This translates into in-depth insights into how the industrial machinery and vehicles with Flash Battery batteries are being used (actual charging/discharging time, days of use, average consumption, temperatures reached, etc.). In addition, the new graphical interface is designed to offer a simpler and even more intuitive and interactive navigation experience.
Artificial intelligence is a true science made up of numerous branches. Among the key technologies used in the latest release of Flash Data Center, it is important to focus on Machine Learning, a subset of artificial intelligence which creates systems that learn from the data analysed and improve the performance.
Why have we chosen to use the most recent Machine Learning techniques?
Our Chief Information Officer, Antonio Gabriele, explains why. He has overseen the development of Flash Data Center since its first version in 2013 and today coordinates our IT team in the development of cutting-edge information technology.
Pictured, from left, are Marco Righi and Antonio Gabriele, respectively CEO & Founder and Chief Information Officer of Flash Battery
“In our case, the concept starts from the complex nature of the battery. We are working with devices that have especially complex chemistry, so Machine Learning enables us to extract from the battery a clear and accurate description of how it is behaving. Our added value lies in the fact that we have collected a huge amount of data on the operation of our batteries. The first Flash Data Center was already in place in 2013 and today we work with an astounding 200 million logs or nearly 100,000 logs a day. Machine learning thrives on data, so this is what sets us apart from the competition.”
In fact, machine learning analyses data using statistical theories and harnesses the processing power of computers to implement every statistical technique. The large amount of data we can provide means that the battery behaviour information extracted is incredibly precise and reliable. We can practically recreate a “digital twin” for each lithium battery and use it for tests and simulations, especially at the design stage, and for formulating and testing behaviour hypotheses for next-generation batteries.
What type of battery data does Flash Data Center analyse?
Flash Data Center analyses all the operating parameters of the lithium battery, specifically:
- SOH (State of Health) of the battery, to get an accurate picture of the condition of every single lithium battery out there in the market.
- Voltage
- Current
- Temperature
- Analysis of charging/discharging times with special attention paid to the minimum and maximum values reached during these activities
A lithium battery can be used in a wide variety of contexts and in many different ways, which all affect its longevity.
Knowing ahead of time where and how to act to extend its life cycle or improve its performance is in itself a great advantage.
Since 2012, we have produced lithium batteries for many very different contexts subject to a variety of stresses. Take, for example, the automated logistics sector, where AGVs and LGVs operate non-stop, 24 hours a day in industrial plants with temperatures ranging from -30°C to +45°C.
Thanks to remote monitoring and predictive data analysis, it is possible to:
- Understand the way in which users make use of lithium batteries
- Estimate the effective battery life on the vehicle or machinery
- Predict how the battery will behave in the future
Three important pieces of information, for us and the customer, who receives accurate planning of replacements and valuable recommendations for correcting and improving the performance of the machinery, which, of course, increases productivity.
But the benefits of remote monitoring and predictive analysis don’t end here! A typical customer that chooses Flash Battery doesn’t install just one lithium battery on its industrial machine or vehicle. We are dealing with complete systems where computer technology, IoT and artificial intelligence have become real allies in ensuring the application stays reliable over time.
-
Correctly sizing the application
Implementing the remote monitoring function right at the prototype stage helps, for example, to size the vehicle more accurately. Analysing the prototype data helps us understand if the application requires a lithium battery that delivers more or less energy or with specific performance-enhancing characteristics.
-
Getting useful information on the actual use of the application
Let’s consider that our customers are usually not the end users of the electrified vehicles. Flash Battery lithium batteries are installed on machines and vehicles that our customers sell all over the world. So, it is clear that having real-time data on their operation is a fast-track way to assess if the end user is using the application correctly (for example, if the vehicle is being exposed to repeated full discharges or out-of-range temperatures).
Let’s use a road sweeper as an example: through constant data monitoring, we can analyse how the battery is performing in that specific usage context, its charge/discharge profile, its limitations, and how the end user is employing it. With this information to hand, the producer can evaluate actual use and implement improvements to its fleets going forward, and we in turn can produce specialist batteries with increasingly better performance.
-
Managing advanced action planning
Lastly, Flash Data Center, with its machine learning-driven automatic data monitoring, allows the advanced planning of extraordinary maintenance work. This avoids unnecessary and expensive machine downtime and lets customers manage the end-of-life of systems independently, meaning they can sustainably plan the replacement of end-of-life lithium batteries in entire fleets and, as a result, optimise and reduce the cost of disposal and make the process of re-using components more efficient.
Today, Flash Data Center can output a very accurate SOH analysis that helps us in our research into increasingly higher-performance and smarter new generation lithium batteries with ad-hoc features for the needs and use of every kind of industrial application.
Its evolution going forward will go hand in hand with the amount of data it will be provided with. We are talking about an intelligent system that is constantly learning, storing and processing. As new data arrives, the system processes and analyses the data; it is always studying and adapting to new data.
“The amount of data we are collecting compared to the past is increasing at a faster and faster rate; today, we are analysing up to 4,000 sensors per lithium battery, and the trend is growing. We are therefore well on our way to building a very sound infrastructure that can continuously process huge amounts of data, interpret trends, variations and anomalies, and reproduce realistic usage scenarios we can use to develop smarter and smarter lithium batteries.”