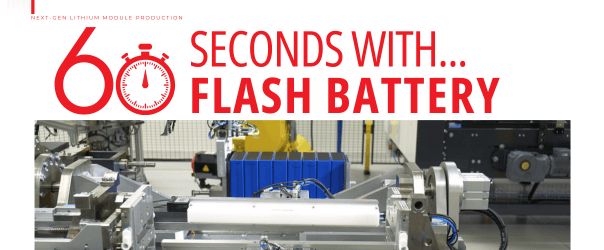
Ground Handling International
60 seconds with Flash Battery
Marco Righi, interviewed by Ground Handling International, talks about Flash Battery's new automated line for module assembly with laser welding.
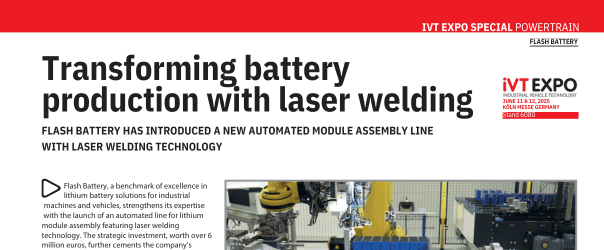
ivt international
Transforming battery production with laser welding
Flash Battery’s production capacity will rise to 90,000 modules per year thanks to the new automated laser welding assembly line. iVT covers the story.
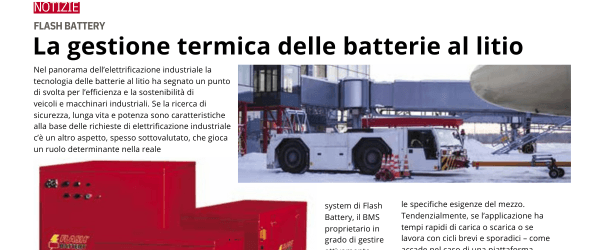
OnSite Construction
Thermal management of lithium batteries
Flash Battery explains to OnSite the benefits of thermal management in a battery and when it’s essential to adopt a heating or cooling system.
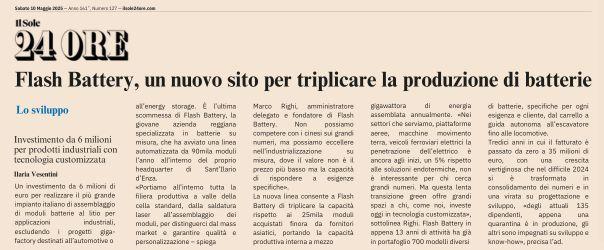
Il Sole 24 ore
Flash Battery, a new site to triple battery production
Flash Battery launches a new automated module assembly line using laser welding technology, bringing module production in-house
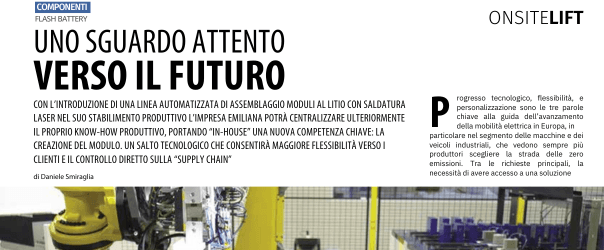
OnSite Lift
A Careful Look Towards the Future
Flash Battery launches its new automated module assembly line with laser welding, centralising its entire production know-how in-house.
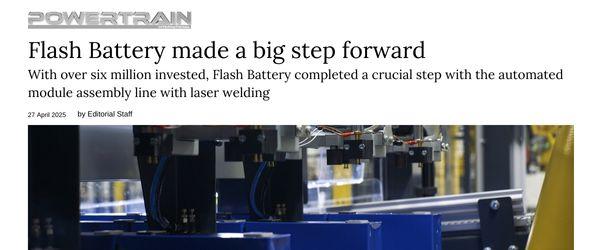
Powertrain International
Flash Battery made a big step forward
With over six million invested, Flash Battery completed a crucial step with the automated module assembly line with laser welding.
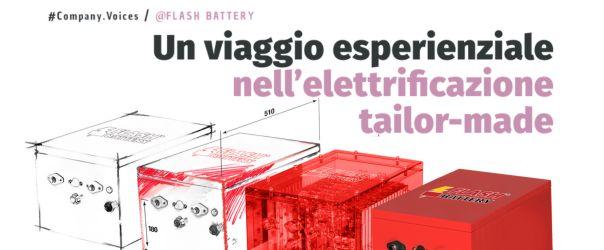
We are access equipment
An experiential journey into tailor-made electrification
At Bauma 2025, Flash Battery leads visitors through lithium battery innovation in an immersive journey unveiling the design process, advanced management system, and tailor-made electrification solutions for the construction sector.
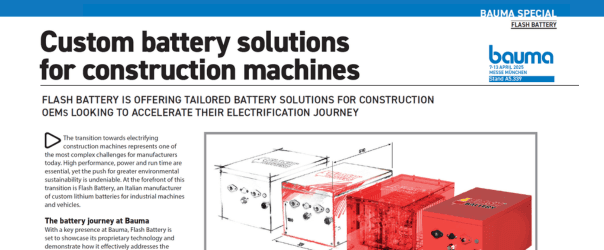
iVT International
Custom Battery Solutions for construction machines
The electrification of construction machinery is advancing rapidly. At Bauma 2025, Flash Battery presents its customised lithium batteries for the sector through an immersive journey into its proprietary technology.