Lithiumzellen: Unterschiede, Verwendungen und wie Man das beste auswählt
23 Januar 2020
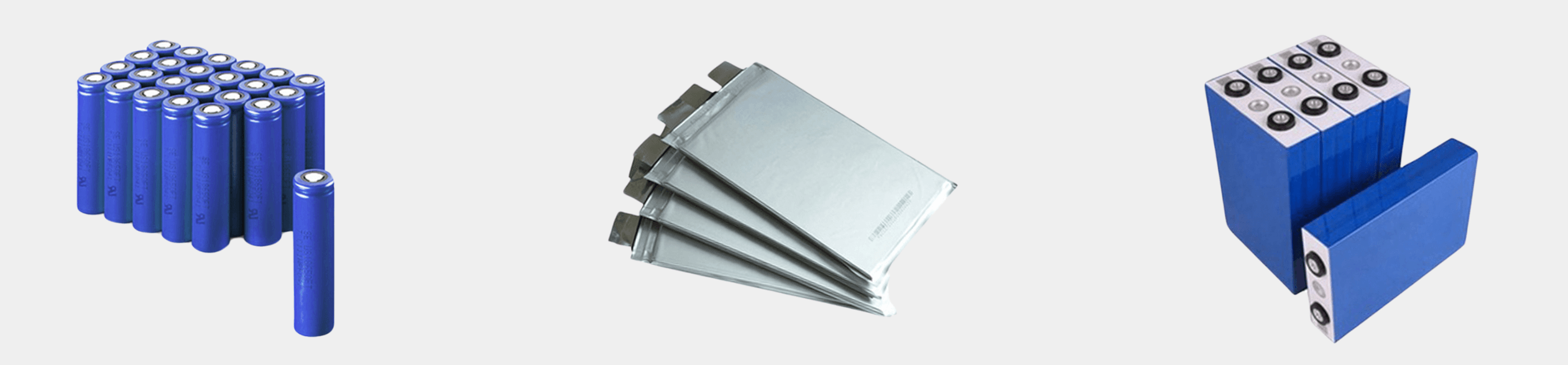
In diesem Artikel werden wir die auf dem Markt erhältlichen Lithiumzellenformate analysieren und herausfinden, welche sich für industrielle Anwendungen am besten eignen.
Ein grundlegendes Elemente der Lithiumbatterien ist sicherlich die Art der Zellen, aus denen sie sich zusammensetzen.
Die heute am häufigsten produzierten Lithiumzellenformate sind 3:
- Zylindrische Zellen
- Pouch-Zellen
- Prismatische Zellen
Die zylindrischen Zellen, die für Lithiumbatterien verwendet werden, sind den Batterien, die wir z. B. in den Fernbedienungen zu Hause haben, sehr ähnlich. Das gebräuchlichste Format ist 18650 (18mm Durchmesser mit 65mm Höhe), es gibt auch andere wie 21700, 26650 oder kundenspezifische Lösungen, die vom Hersteller der Zellen selbst gewählt werden.
Vorteile der zylindrischen Zellen
Die Vorteile der Verwendung von zylindrischen Lithiumzellen sind das strapazierfähige Gehäuse und die Möglichkeit, die Chemie zu wechseln, während der Behältnismechanismus unverändert bleibt.
Beispiel für zylindrische Zellen
Nachteile der zylindrischen Zellen
Die negativen Aspekte der zylindrischen Lithiumzellen sind die geringe Kapazität der Einzelzelle: sie erreichen ein Maximum von 3 Ah und die Zellen werden in Serie und parallel durch Löten zusammengefügt. Bei dieser Art der Konstruktion ist es nicht möglich eine einzelne Zelle auszutauschen, sondern diese erfordert den Austausch eines ganzen Moduls mit aufwändigen und teuren Eingriffen. Wenn Ihr Industriefahrzeug ein Problem an der Batterie meldet, müssen Sie das gesamte Modul austauschen und es kommt zu kostspieligen Ausfallzeiten. Darüber hinaus führt die geringe Kapazität der einzelnen Elemente und die daraus resultierende „Parallelschaltung“ vieler Elemente oft zu einer Beeinträchtigung der Sicherheit des gesamten Lithiumbatteriepacks.
Beispiel.
Die meisten Hersteller von Lithium-Ionen-Batterien setzen, um die gewünschte Kapazität zu erreichen, eine Anzahl von Zellen parallel. Will man zum Beispiel eine Kapazität von 200 Ah mit 2,5 Ah Zellen erreichen, müssen 80 Zellen parallel angeordnet und geschaltet werden. Schließt eine davon wegen einem internen Problem kurz, wird sie nicht nur ihre Energie absorbieren, sondern auch die gesamte Energie der 80 parallelen zylindrischen Zellen.
Dieses Phänomen könnte zu einer sehr hohen Hitze im Modul führen, die auch katastrophale Auswirkungen haben könnte, z. B. ein Brand. Um dies zu vermeiden, verwenden große Hersteller wie Tesla sehr ausgeklügelte Produktionsverfahren, die es erlauben, die Zellen mit einer Art Sicherung parallel zu schalten. Bei einem Kurzschluss einer Zelle brennt die „Sicherung“ durch und das Batteriepack bleibt sicher.
Leider gibt es jedoch keine Hersteller von Lithiumbatterien auf dem industriellen Markt, die über diese Technologien verfügen. Diese negativen Aspekte haben uns veranlasst, diesen Zellentyp in den Flash Battery-Batterien nicht zu verwenden.
Bei den Lithium-Pouch-Zellen, die wegen ihrer Bauform als Paket/Beutel so genannt werden, ändern sich die Abmessungen je nach den Konstruktionsentscheidungen des Herstellers sehr stark.
Vorteile der Pouch-Zellen
Die positiven Aspekte dieser Lithiumtechnologie sind die hohe erreichbare Energiedichte und die niedrigen Kosten des Gehäuses. Auf dem Markt finden sich Pouch-Zellen von einigen hundert mAh bis zu 20 Ah; es gibt nur sehr wenige Hersteller, die diesen Grenzwert überschreiten.
Beispiel für Pouch-Zellen
Nachteile der Pouch-Zellen
Der negativste Aspekt ist sicherlich die Zerbrechlichkeit der Hülle, bei der es nicht viel braucht, um zu brechen, selbst mit einem Nagel kann man sie irreparabel beschädigen. Bei der Verwendung dieses Typs von Zellen ist das Zellverpackungssystem maßgeblich, das jede Art von Stress für die einzelnen Zellen verhindern muss: Vibrationen, Quetschungen und Verformungen.
Das Zellverpackungssystem für die Erstellung der Module ist sehr wichtig, deshalb ist es kompliziert, wenn nicht gar unmöglich, kundenspezifische Module herzustellen.
Die Zellen haben immer eine geringe-mittlere Kapazität. Um industrielle Batteriepacks herzustellen würde man Dutzende von Zellen parallel benötigen, was die Sicherheit des Batteriepacks verringert. Auch in diesem Fall werden die einzelnen Zellen gelötet, um sie in Reihe oder parallel zu verbinden. Eine einzelne Zelle ist somit nicht zu ersetzen und es muss das gesamte Modul ausgetauscht werden.
Die prismatischen Lithiumzellen haben ein solides Gehäuse, normalerweise aus Kunststoff oder Metall (Aluminium), mit Schraub- oder Lötanschlüssen.
Vorteile der prismatischen Zellen
Das Gehäuse der prismatischen Zellen ist sehr strapazierfähig, daher eignet sich sehr gut für die Herstellung kundenspezifischer Batteriepacks ohne aufwendige Studien und teure Tests zur mechanischen Belastung.
Dank der hohen Kapazität der einzelnen Elemente erhält man bis zu 300 Ah in einer Zelle. Das ist vor allem bei der Herstellung von Batterien mit hohen Kapazitäten, wie der industrielle Markt sie benötigt, sehr geschätzt. Parallele Zellen werden somit vermieden und die Sicherheit des gesamten Batteriepacks erhöht. Ein weiterer wichtiger Aspekt sind die schraubbaren Polklemmen, die die Montage vereinfachen und den Austausch eines Elements auch vor Ort erleichtern.
Nachteile der prismatischen Zellen
Der Nachteil der prismatischen Lithiumzellen ist die etwas geringere Energiedichte aufgrund der Bauform.
Beispiel für prismatische Zellen mit Aluminiumgehäusen
Wenn man versucht, die Informationen über die oben genannten Lithiumzellen zusammenzufassen, könnte man das sagen:
- Zylindrische Zellen werden normalerweise in kleinen Lithiumbatterien (< 2 kWh), z. B. in Elektrofahrrädern, Schraubendrehern, Geräte für die Pflege von Grünflächen, etc. ...) verwendet, nur Tesla verwendet sie im Automobilbereich.
- Pouch-Zellen werden hauptsächlich mit der NMC-Chemie hergestellt und vor allem bei Anwendungen mit hoher Leistung (hohe Spannung und niedrige Kapazität) oder bei Anwendungen, bei denen es notwendig ist, das belegte Volumen zu reduzieren, z. B. bei Elektromotorrädern oder Elektroautos, eingesetzt.
- Prismatische Zellen werden für Lithiumbatterien in der Industrie und im Automotivebereich zur Herstellung von mittelgroßen und großen Batteriepacks verwendet.
Gerade wegen ihrer Eigenschaften haben wir uns bei den Flash Battery-Batterien für prismatische Zellen entschieden.
Sie ermöglichen es uns, qualitativ hochwertige Leistungen sowohl bei Industriemaschinen als auch bei Elektrofahrzeugen zu erzielen.
Erfahren Sie mehr über unsere Technologie und wer sich bereits für die meistverkaufte Lithiumbatterie in Italien entschieden hat.