Recyclage des batteries au lithium: quelques explications
22 décembre 2020
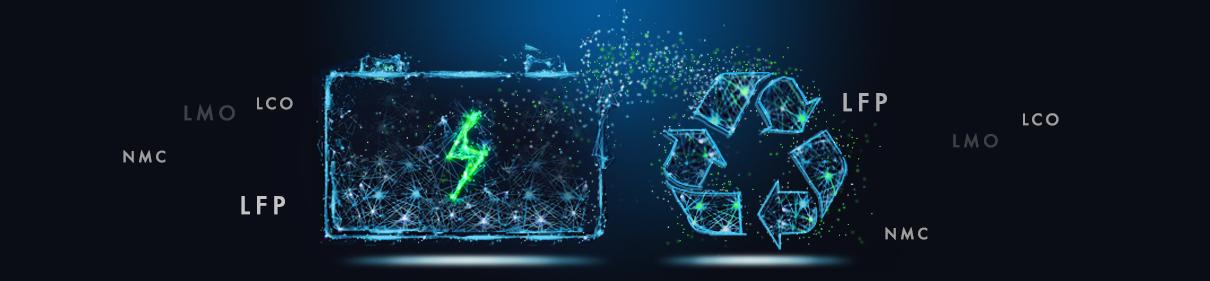
Le lithium représente de nos jours l’un des éléments les plus importants en vue de la transition vers la mobilité électrique et certains problèmes tels que l’élimination et la récupération des accumulateurs lithium-ion à la fin de leur vie utile deviennent de plus en plus pressants. En effet, la production d’accumulateurs au lithium-ion ne fait qu’augmenter, en conséquence de quoi, dans les années à venir, les accumulateurs qui arriveront à la fin de leur service et qui devront être éliminés seront de plus en plus nombreux. Un recyclage approprié de ceux-ci s’avère donc essentiel, car ils peuvent contenir divers métaux de grande valeur, ainsi que d’autres substances qui, si elles ne sont pas correctement traitées, risquent de nuire à l’environnement.
Pour pouvoir approfondir le problème du recyclage d’un accumulateur lithium-ion, il convient de partir du début et d’analyser tout d’abord la manière dont est composée la structure de l’accumulateur ainsi que tous les éléments qui le composent.
Fig. A: How Lithium-ion batteries work – Credits: Sarah Harman and Charles Joyner [1]
La structure classique d’une cellule lithium–ion est formée de :
- une cathode – c’est-à-dire le pôle positif de l’accumulateur, constituée d’un matériau cathodique (par exemple LFP, NMC, LMO, LCO) et par le collecteur de courant (généralement en aluminium)
- une anode – c’est-à-dire le pôle négatif de la batterie, constituée par un matériau anodique (par exemple graphite, carbone, LTO) et par le collecteur de courant (généralement en cuivre)
- un séparateur – généralement polymérique et céramique qui est interposé entre la cathode et l’anode, en exerçant une fonction d’isolation (iI sert donc à éviter un court-circuit interne)
- l’électrolyte contenant un sel de lithium (par exemple, LiPF6). L’électrolyte remplit tout le volume à l’intérieur de la cellule, en mouillant les électrodes et en permettant le transport d’ions de l’anode à la cathode et inversement, en passant par les pores du séparateur.
- des additifs, qui ont pour mission de faciliter le transport d’ions lithium d’une électrode à l’autre au cours des processus de chargement et de déchargement de la cellule, en protégeant les électrodes elles-mêmes (par exemple, carbonate d’éthylène (EC) et diméthyl carbonate (DMC).
FIG. B: Exemple de structure d’une cellule prismatique – le type de cellules utilisé par Flash Battery [2]
Les accumulateurs lithium-ion, bien qu’ils présentent une durée de vie beaucoup plus longue que les accumulateurs classiques, se détériorent au fil du temps et de leur utilisation, ce qui diminue leur capacité de stockage d’énergie (Ah et Wh) et leur capacité de fournir des pics de courant (A et W).
L’usure et la détérioration de l’électrolyte, de même que des matériaux anodiques et cathodiques, ont inexorablement pour conséquence que les accumulateurs au lithium présentent une durée de vie qui est en partie préétablie et qui dépend, d’autre part, des conditions d’utilisation (température, courants de charge et de décharge, limites de tension d’utilisation).
L’énergie électrique fournie par les accumulateurs au lithium a connu une augmentation sans précédent au cours de ces dernières années et, du fait de cette demande croissante d’accumulateurs, on assiste à une augmentation progressive de la demande de minerais, ainsi qu’à une exploitation de plus en plus intensive des gisements (respectivement 35 % et 25 % du lithium et du cobalt extraits sont utilisés pour produire des accumulateurs au lithium [3] ) ces deux minerais étant cependant en train d’atteindre leurs limites d’extraction, ce qui a pour effet d’accroître considérablement l’impact de l’extraction sur l’environnement.
C’est pourquoi la récupération de l’accumulateur au lithium présente un intérêt de plus en plus grand, surtout si on tient compte de la quantité d’accumulateurs qui seront produits et éliminés dans les années à venir. En effet, les ressources disponibles à partir du recyclage peuvent s’avérer considérables, en plus d’atténuer un facteur de pollution et de compenser partiellement la rareté des ressources du territoire.
Le recyclage des accumulateurs lithium-ion peut donc constituer une ressource stratégique permettant de limiter une certaine vulnérabilité dans l’approvisionnement en matériaux.
Le développement des nouvelles générations de cellules tient largement compte de ces facteurs, en réduisant le pourcentage de cobalt, mais il existe aussi des produits chimiques au lithium, comme celui qui est principalement utilisé par Flash Battery (LFP), qui est entièrement exempt de cobalt. La technologie LFP, la plus sûre et la plus stable que l’on puisse trouver sur le marché, garantissant une durée de vie extrêmement longue (plus de 4.000 cycles de recharge) est en effet également plus sûre à recycler et présente un impact modéré sur l’environnement.
L’Europe n’arrive pas encore à jouer un rôle clé dans le recyclage des accumulateurs au lithium. Il suffit de savoir qu’au cours de la période 2013-2014, sur un total de 65.500 tonnes d’accumulateurs au lithium, seules 1.900 tonnes ont été récupérées en Europe, ce qui a entraîné la perte de précieuses ressources, tant financières que du point de vue des minéraux eux-mêmes.
À l’heure actuelle, l’écart dans le recyclage s’est considérablement réduit, mais globalement, il ne dépasse pas encore 50 %, un taux qui est surtout le fait de la Chine et de la Corée du Sud, où la plupart des tonnes d’accumulateurs usés finissent aujourd’hui leur cycle de vie. En effet, au niveau mondial, en 2018, 97.000 tonnes ont été recyclées, dont 67.000 en Chine, 18.000 en Corée du Sud et le reste en Europe.
On estime qu’il sera possible, en 2030, de récupérer entre 400 et 500 millions d’euros, (en tenant compte des prix actuels) rien qu’en ce qui concerne l’aluminium, le cobalt, le nickel et le lithium[4] . En outre, on estime qu’en 2025, les accumulateurs qui arriveront en fin de vie constitueront environ 800.000 tonnes de minéraux à éliminer et à récupérer.
Fig. C : Poids total de batteries au lithium disponibles pour le recyclage dans le monde[5]
À l’heure actuelle, le processus d’élimination et de recyclage d’une batterie au lithium est principalement dicté par la valeur marchande de ses composants et par la disponibilité de ceux-ci dans les centres de recyclage.
C’est pourquoi l’aluminium, le cuivre et le cobalt sont les éléments les plus intéressants en Europe (en particulier en Allemagne, où sont situés la plupart de ceux qui exercent ce genre d’activité de nos jours), car ils sont récupérés sous la forme d’alliages métalliques « black mass » (ensemble de tout ce qui est mis sous fusion) qui exigent un certain nombre d’étapes supplémentaires pour la production de matériaux directement utilisables pour les nouveaux accumulateurs.
Fig. D : Évaluation des capacités de recyclage en Europe à l’horizon 2019 [6]
En Chine et en Corée du Sud, par exemple, le lithium est principalement récupéré sous forme de carbonate de lithium (Li2CO3) et les matériaux anodiques et cathodiques sont recyclés plus efficacement grâce à l’abondance des déchets disponibles. En effet, 70 % des études sur le recyclage ont été réalisées à ce jour par la Chine et la Corée du Sud, où tous les matériaux actifs sont en mesure d’être recyclés avec des rendements élevés et où la récupération globale des matériaux est déjà supérieure à 90 %. [7]
Fig. E : Quantité d’accumulateurs u lithium recyclés (en tonnes)[5]
Le procédé idéal de recyclage d’un accumulateur lithium-ion devrait permettre de récupérer la quasi-totalité des composants des accumulateurs et on prévoit que cette récupération dépassera 95 % de leurs composants dans un avenir très proche. Malheureusement, comme on a déjà eu l’occasion de dire, le problème du traitement des accumulateurs éliminés est encore en cours de définition au niveau mondial :
- des règlements précis font défaut
- des centres et des structures spécialement prévus pour l’élimination des accumulateurs sont encore en voie de développement
Pourquoi ?
La principale raison en est que le secteur des accumulateurs lithium-ion est encore relativement jeune et que ceux-ci présentent en outre une durée de vie plutôt longue ; par conséquent, les volumes d’accumulateurs à recycler sont encore très faibles aujourd’hui et ne justifient pas de véritables investissements pour la création de centres de recyclage (souvent très onéreux : en effet, recycler le lithium et les autres matériaux qui constituent les accumulateurs peut en arriver à coûter plus cher que l’achat de la source primaire).
Néanmoins, les grands chefs de file du secteur sont en train d’adopter des mesures permettant d’organiser une production se basant sur des principes de recyclabilité, en adhérant aux consortiums de recyclage existant sur les territoires nationaux et en étudiant les possibilités de recourir à de matériaux de plus en plus faciles à recycler.
Le rôle de COBAT dans l’élimination des accumulateurs
Flash Battery, par exemple, a d’ores et déjà adopté des mesures permettant de se conformer aux obligations légales en vigueur en vertu du décret législatif (ordonnance) italien 188/08 et ses amendements ultérieurs, en adhérant, dès 2015, au consortium COBAT (Consortium national collecte et recyclage) visant à la gestion, l’élimination et le recyclage des piles et des accumulateurs.
Tous les trimestres, les entreprises italiennes qui sont inscrites au consortium COBAT sont tenues de verser des contributions proportionnelles au nombre d’accumulateurs qu’elles introduisent sur le territoire italien, ceci étant destiné à financer le système de recyclage des accumulateurs, qui prendra son véritable essor dans les années à venir.
La responsabilité du recyclage des accumulateurs qui sont introduits sur le marché étranger incombe à ceux qui importent l’accumulateur dans leur propre pays et ils devront appliquer de manière scrupuleuse les réglementations et les lignes directrices adoptées dans leur propre nation en cette matière.
Au sein de l’Union européenne, la collecte et le recyclage des piles et accumulateurs sont régis par la directive 2006/66/CE (appliquée en Italie par le biais du décret législatif (ordonnance) 188/08, ainsi que ses amendements ultérieurs), qui prévoit que les États membres doivent adopter toutes les mesures qui sont nécessaires pour optimiser et promouvoir la collecte sélective, en évitant que ces produits ne soient éliminés en tant que déchets municipaux mixtes. Cela implique la mise en place de systèmes appropriés permettant de déposer les piles et accumulateurs usagés auprès de points de collecte situés à proximité des utilisateurs et de les récupérer gratuitement auprès des producteurs.
La directive 2006/66/CE a aujourd’hui pour objectif le recyclage des accumulateurs lithium-ion retirés du service, à concurrence d’au moins 50 % du poids, en finançant leur collecte, leur traitement et leur récupération. Malheureusement, pour garantir la durabilité à long terme, Il faudrait atteindre des objectifs beaucoup plus élevés (les 95 % évoqués ci-dessus).
C’est précisément pour cette raison que, ces dernières années, les nouvelles technologies au lithium seront produites sur la base de critères de plus en plus précis pour ce qui est de :
- Conception durable: au cours de la construction des accumulateurs, on évitera l’utilisation de matériaux nuisibles à l’environnement (par exemple, le cobalt) et, au niveau de la production, on visera à optimiser ou à éliminer les étapes particulièrement polluantes, au niveau de la production (exemple : passer d’un dépôt en phase liquide, dans lequel on a recours à des solvants organiques volatils à un procédé directement effectué en phase solide ou semi-solide, dans le cadre duquel la quantité de solvants est considérablement réduite, ce qui a pour effet que les processus d’évaporation de ces solvants sont eux aussi minimisés, ce qui entraîne des économies d’énergie).
- Conception pour le démantèlement: du point de vue mécanique, l’accumulateur sera réalisé en vue d’être facilement prélevé et ouvert, afin d’accélérer le processus de démantèlement (par exemple, conception mécanique souple).
- Conception pour le recyclage: au niveau des matériaux utilisés, les accumulateurs seront conçus en tenant compte, dès le début, du fait qu’ils devront être recyclés en fin de vie (par exemple, utilisation de matériaux à base d’eau plutôt qu’organiques).
La mission que Flash Battery s’est donnée : des accumulateurs lithium de plus en plus recyclables
Le service de recherche-développement de Flash Battery mène à bien une recherche incessante de matériaux de plus en plus recyclables et, en même temps, hautement performants, qui garantissent la plus grande efficacité de la part de l’accumulateur lithium, tout en tenant compte de la durabilité et du faible impact environnemental.
En effet, dès 2017, Roberto Nasi, Materials Engineer de notre service de R&D, exprimait dans cet extrait d’article du « Journal of Solid State Electrochemistry » l’importance d’alternatives éco-viables dans le cadre des processus de production des accumulateurs lithium-ion :
La technologie actuelle du lithium-ion, lors de la phase de production industrielle des électrodes, présente l’inconvénient d’utiliser des matériaux polluants et sans aucun doute coûteux, tels que le poly (fluorure de vinylidène) (PVDF), un polymère largement utilisé en tant que liant des matériaux qui constituent les électrodes de la cellule, ce à quoi s’ajoute la nécessité d’utiliser comme solvant le N-Méthyl-2-pyrrolidone (NMP), un solvant très toxique et lui aussi coûteux.
Ces matériaux, en plus de présenter des procédures de recyclage malaisées, posent également des problèmes en raison des normes strictes qui régissent leur utilisation et des coûts qui découlent de la nécessité d’éliminer une partie de ces matériaux lors des phases de séchage des électrodes.
Il est donc souhaitable de remplacer ces matériaux par d’autres produits dans le cadre du cycle de production. Une des voies qu’il serait possible de parcourir, en vue de parvenir à un processus respectueux de l’environnement, consiste en l’introduction, dans les processus de production, de matériaux qui peuvent être traités dans l’eau plutôt que dans des solvants organiques.
En effet, ces dernières années, les efforts ayant été déployés pour trouver des solutions permettant d’éviter le recours à ces matériaux toxiques ont conduit à l’étude de différents systèmes de liants solubles dans l’eau, y compris les gommes, la carboxyméthylcellulose (CMC), l’acide polyacrylique (APP) et le poly(alcool vinylique) (APV) [8]
L’engagement pris par l’Italie en faveur de la récupération des accumulateurs au lithium
Bien que le problème du recyclage soit encore à un stade embryonnaire, tout particulièrement en Europe, il convient de souligner que l’engagement des chercheurs et des grands chefs de file internationaux dans la production et la conception d’accumulateurs lithium-ion s’est tout particulièrement orienté vers ce genre de problème, non seulement en termes de production écodurable, mais aussi en termes de nouvelles possibilités d’approvisionnement en matières premières.
En fait, nous rappelons que la Commission européenne a approuvé, en vertu des règles de l’UE relatives aux aides d’État, un projet important d’intérêt européen commun “IPCEI” notifié conjointement par la Belgique, la Finlande, la France, l’Allemagne, l’Italie, la Pologne et la Suède, visant à soutenir la recherche et l’innovation dans le secteur prioritaire européen commun des batteries.
European Commission: IPCEI
L’Italie, par exemple, est en première ligne dans l’étude d’une nouvelle technologie : le consortium COBAT, conjointement avec le CNR-Iccom de Florence, a récemment lancé un brevet technologique avec procédé hydro-métallurgique, qui permet une récupération plus efficace des métaux contenus dans les batteries telles que le lithium, le cobalt et le manganèse.
Pourquoi cette exigence ?
Non seulement pour accroître le recyclage en faveur de l’environnement, mais aussi parce que notre continent manque de lithium et de métaux rare : si nous étions contraints, en Europe, de nous appuyer exclusivement sur nos propres ressources en minerais, nous ne serions pas en mesure de répondre aujourd’hui de manière efficace à la demande du marché.
C’est la raison pour laquelle nous devons recycler les métaux afin de réduire notre dépendance à l’égard de la Chine et de la Corée du Sud, deux pays qui possèdent actuellement la suprématie dans le secteur de la production des cellules des accumulateurs.
Bibliographie
[1] https://www.energy.gov/eere/articles/how-does-lithium-ion-battery-work
[2] https://www.degruyter.com/view/journals/psr/3/11/article-20170111.xml
[3] Golmohammadzadeh, R.; Faraji, F.; Rashchi, F. Recovery of lithium and cobalt from spent lithium ionbatteries (LIBs) using organic acids as leaching reagents: A review.Resour. Conserv. Recycl.2018,136,418–435
[4] Drabik and Rizos, 2018
[5] https://circularenergystorage.com/
[6] Lebedeva et al, 2017; Dallöf et al, 2019; Lv et al., 2018; Neometals, 2019; Redux, 2019; Umicore, 2019; uRecycle, 2019
[7] https://www.duesenfeld.com/index.html
[8] Nasi, R., et al. New eco-friendly low-cost binders for Li-ion anodes. J Solid State Electrochem 21, 3429–3435 (2017). https://doi.org/10.1007/s10008-017-3665-5